Fluchtverhalten
Beim Edelstahl-Kugelstrahlen von sehr leichten und kleinen Bauteilen in der Muldenbandstrahlanlage kommt es häufig vor, dass Bauteile während des Strahlprozesses fluchtartig den Strahlraum verlassen und auf das darunterliegende Sieb fallen. In großer Zahl auf dem Sieb liegend blockieren sie dieses und verhindern so den Rücktransport des Strahlmittels. Außerdem ist die Oberfläche der heruntergefallenen Bauteile nicht ausreichend gestrahlt, weil sie ja nicht über die vorgesehene Dauer bearbeitet wurden.
Ursachenforschung
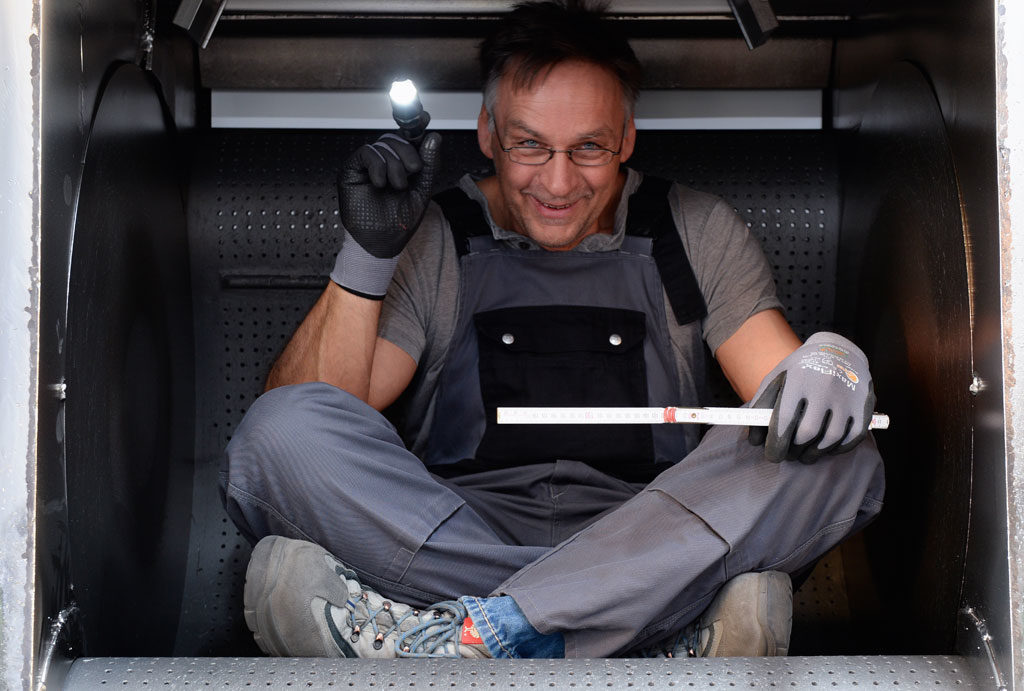
Um die Ursache zu finden, muss man auch mal unbequeme Dinge auf sich nehmen. Ich steige also mit Taschenlampe, Gliedermaßstab (Zollstock) und Fotoapparat in das Innere der Muldenbandanlage und lasse die Tür von außen schließen. Chef eingesperrt – Einzelhaft. Für die Mitarbeiter eine gute Gelegenheit den Lohn neu zu verhandeln. Die kommen aber gar nicht auf die Idee – Glück gehabt. Das Problem ist bei geschlossener Tür sofort sichtbar: Zwischen der Prallplatte und der Oberkante des Muldenbandes bleibt ein ca. 4 cm breiter Spalt, durch den die Bauteile durchrutschen können. Dieser Spalt müsste während des Strahlprozesses so gut es geht verschlossen werden, am besten mit einer verschleißfesten Dichtung.
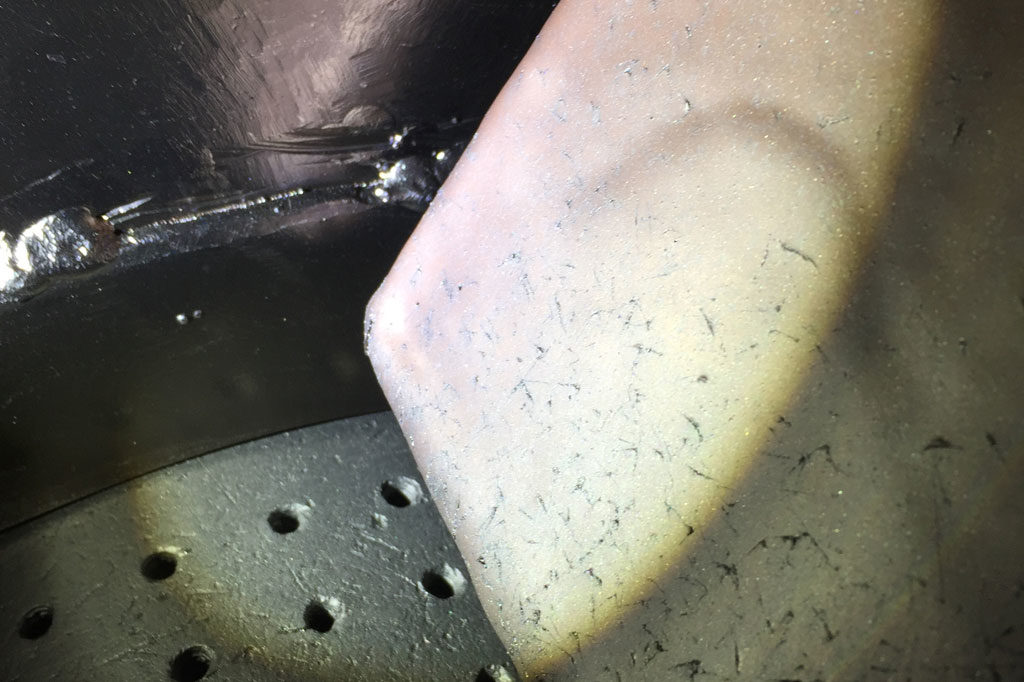
Auf dem Foto ist das leider sehr schlecht zu erkennen, aber der Spalt zwischen der Unterkante der Prallplatte und dem gelochten Gummiband ist ca. 4 cm hoch und geht über die gesamte Breite des Muldenbandes.
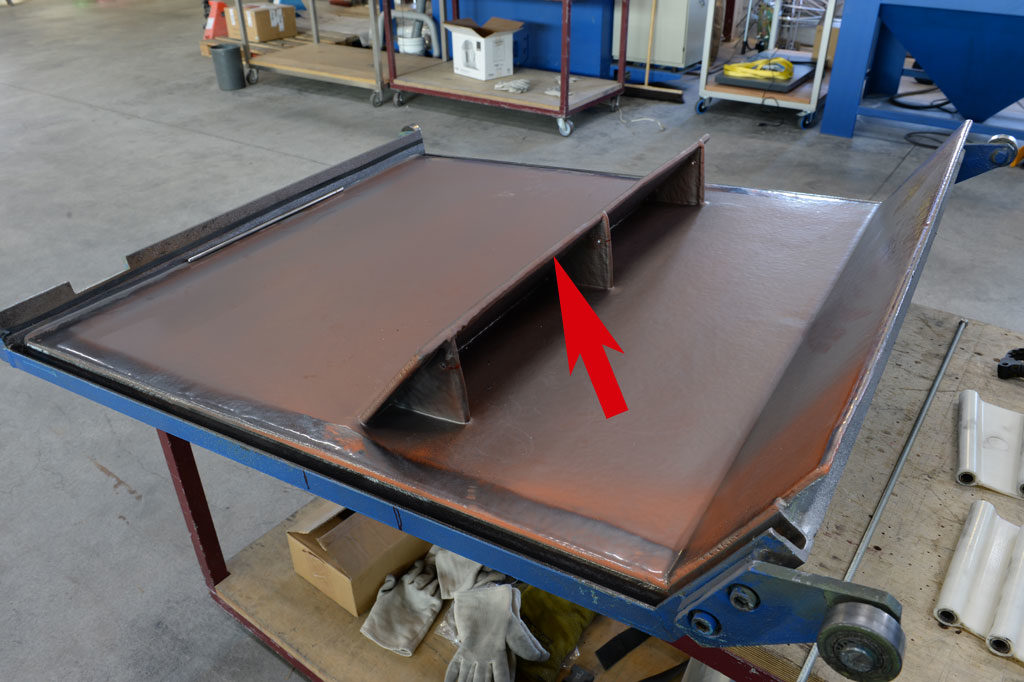
Die demontierte Tür der Muldenbandstrahlanlage auf dem Rücken liegend: Die Prallplatte ist über Dreiecksbleche mit der Tür verschweißt. Diese Bleche lassen sich gut zur Montage einer elastischen Dichtung nutzen.
Entwurf der Dichtlippe
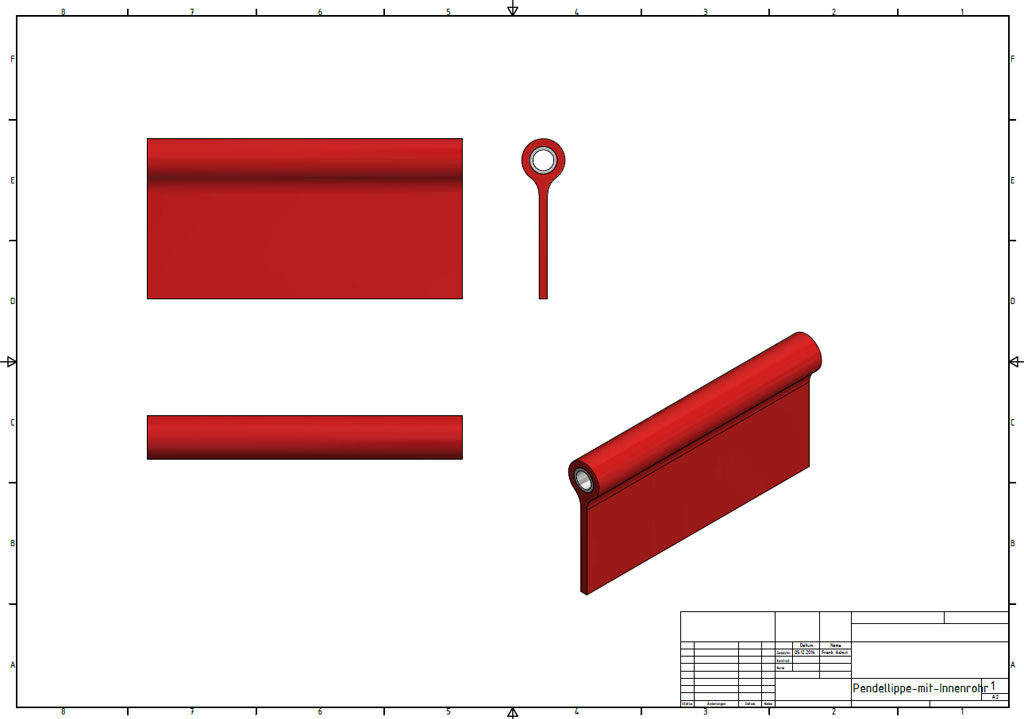
Eine pendelnd aufgehängte Dichtlippe sollte das Problem beheben können. Mit den noch vorhandenen PU-Materialien aus dem letzten „Polyurethan gießen“ – Projekt müsste sich so etwas anfertigen lassen.
Modellbau
Ich baue ein Musterteil aus Plexiglasresten für die Erstellung einer Gießform. Die Zapfen an den Enden des Rundstabes entstehen an der Drehmaschine und sollen später beim Gießen die Aufnahme des Innenrohres möglich machen. Der Übergang zum flachen Teil wird mit 2-K Polyesterspachtel gefüllt. Ein auf einen weiteren Rundstab aufgeklebtes Stück Schleifpapier sorgt für den passenden Übergang.
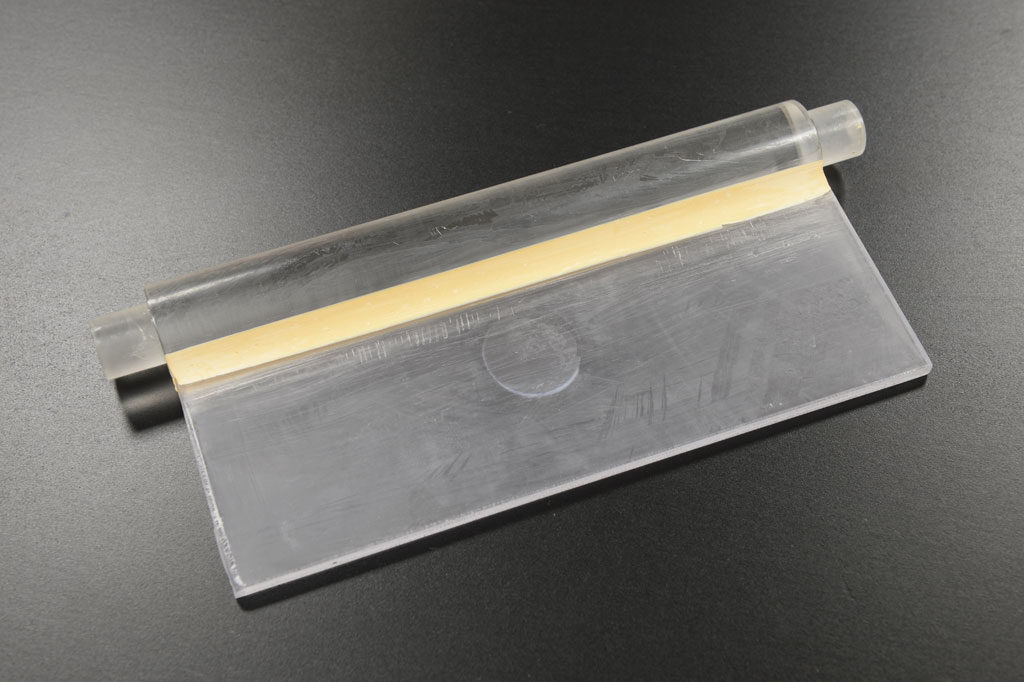
Dieses Modell aus Plexiglas klebe ich auf einen kleinen runden Sockel und diesen auf die Grundplatte des Gießformrahmens. Davon gibt es leider kein Foto. Der Rahmen ist wieder ein alter Bekannter aus dem Schutzkappen-Projekt.
Formbau
Im nächsten Bild ist die erste Formhälfte bereits gegossen. Ich habe mal einen Tropfen PUR-Abtönpaste Rot G 10 in die A-Komponente gegeben. Das PU habe ich dann vorsichtig so am Modell vorbei gegossen, dass es von unten bis zur Hälfte des Modelles ansteigen konnte.
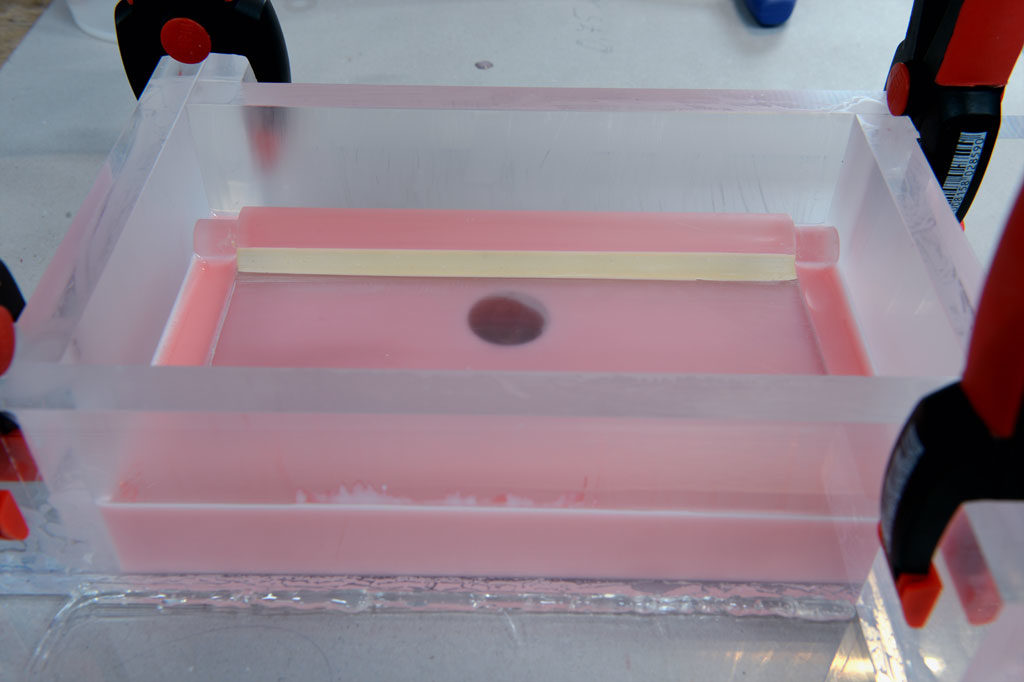
In die ausgehärtete untere Formhälfte habe ich Sacklöcher gebohrt. In diesen Sacklöchern entstehen beim Gießen der oberen Formhälfte Zapfen, welche die beiden Hälften später genau zueinander ausrichten. Formenbauer nennen diese Punkte auch Schlösser. Nach dem erneuten Einpinseln mit Trennmittel wird die obere Formhälfte gegossen. Diesmal mit 2 Tropfen PUR-Abtönpaste Rot G 10 in der A-Komponente.
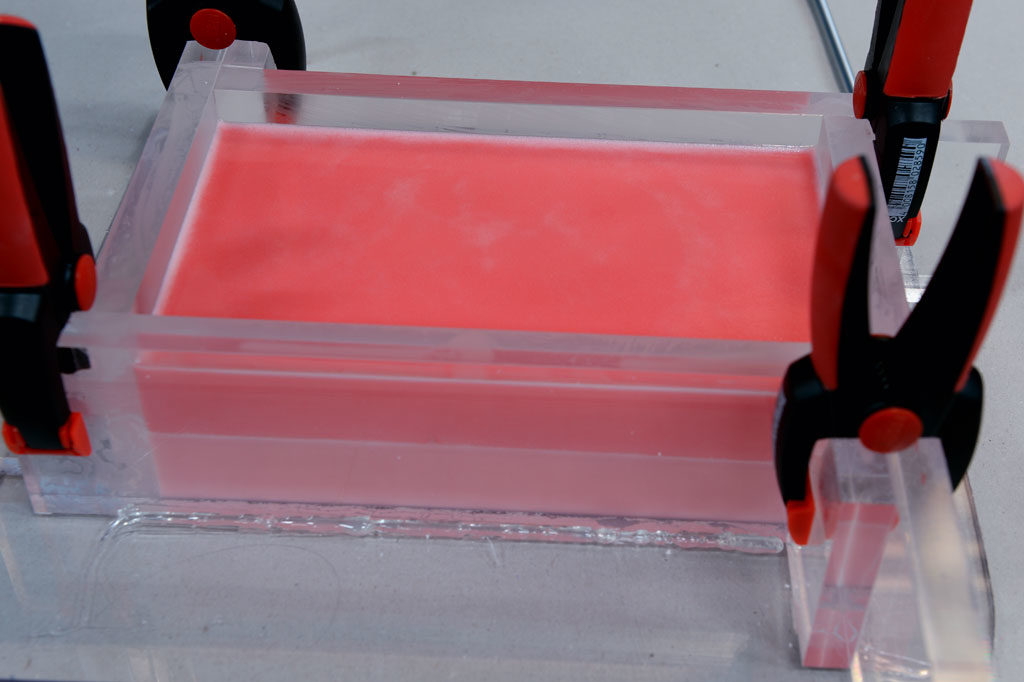
Das nächste Bild zeigt beide Formhälften und das Plexiglas-Modell nach dem Entformen. Die Zapfen der oberen Formhälfte passen exakt in die Sacklöcher und halten beide Hälften genau in der richtigen Position zueinander. Jetzt kann die erste Dichtlippe entstehen.
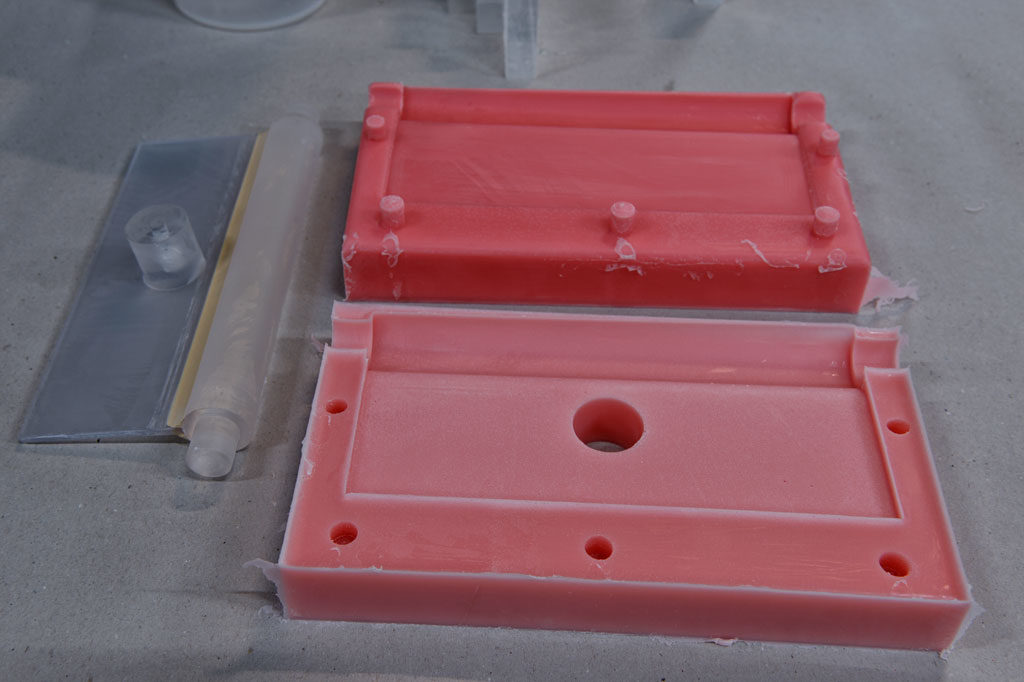
Die beiden Formhälften sprühe ich dünn mit Silikon-Trennmittel ein. Erst danach wird das Innenrohr eingelegt – möglichst ohne es mit Trennmittel zu benetzen. Das Innenrohr habe ich zur Verbesserung der Haftung vor dem Eingießen mit Korund gestrahlt. Auf der rauen Oberfläche haftet das Polyurethan besser. Außerdem muss der Sockel in der unteren Formhälfte bleiben.

Guss
Das Endprodukt hat ein berechnetes Harzvolumen von 120 ml. A- und B-Komponente werden, verwendet man Elastocoat C 6905, in einem Gewichtsverhältnis von 100:32 gemischt. Ich versuche ca. 170 g Vergussmasse anzusetzen, weil sich die Mischbecher nie restlos entleeren lassen. Das gelingt natürlich aus einem 5-Liter-Kanister nicht immer auf den Punkt. Ich peile 130 Gramm A-Komponente an. Wenn es dann auf der Waage 133,5 g sind, passe ich die Härtermenge in einem Extrabecher an. In diesem Fall wären das 42,7 g.
Ich passe also die berechneten Mengen in jeweils eigenen Bechern genau an, bevor ich anfange sie zu vermischen. Meist gieße ich den dünnflüssigen Härter in die dickere Harzkomponente. Trotzdem verbleibt ein Rest von ca. 3 Gramm im Härterbecher. Es kann also nicht schaden 3 Gramm mehr Härter abzuwiegen als man benötigt.
Ein Angusstrichter war nicht vorgesehen. Ich habe einfach mit einem Skalpell einen Teil des äußeren Formrandes entfernt und gieße das Polyurethan in die so entstandene Öffnung.
Nach dem Gießen braucht das Polyurethan Ruhe – am besten lässt man es über Nacht gründlich durchhärten. Am nächsten Morgen kann dann die erste Dichtlippe entformt werden.
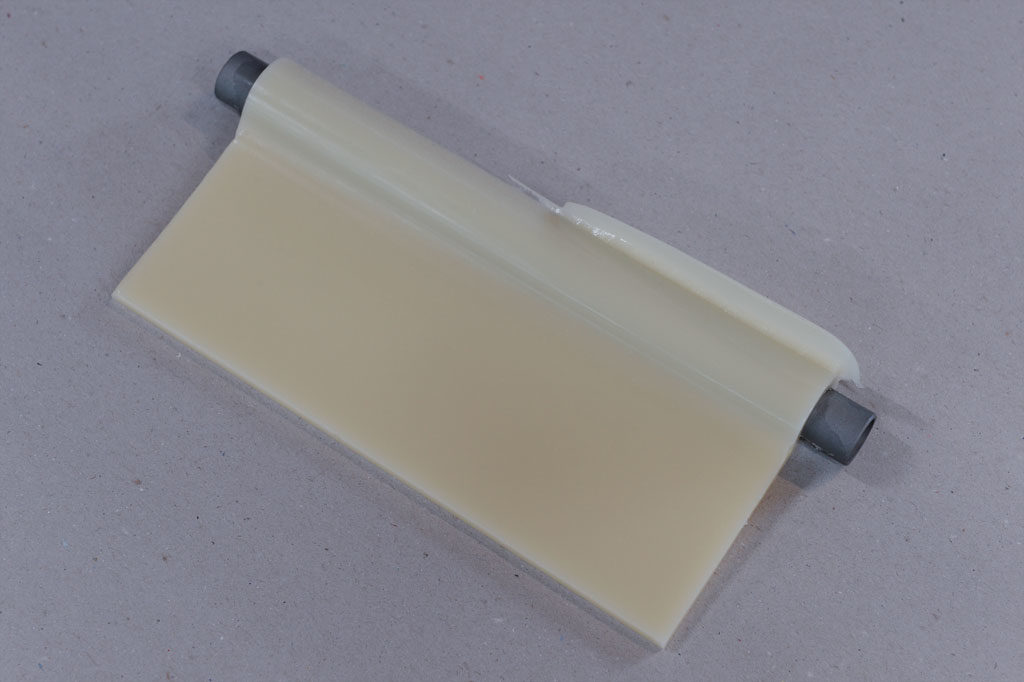
Nach dem Abschleifen des Angusses und der überstehenden Rohrenden sind die Dichtlippen zum Einbau in die Tür bereit. Sie werden einfach über eine Gewindestange zwischen die Dreiecksbleche montiert. Sie sind pendelnd aufgehängt und sollten jetzt bei geschlossener Tür bis auf das Muldenband reichen.
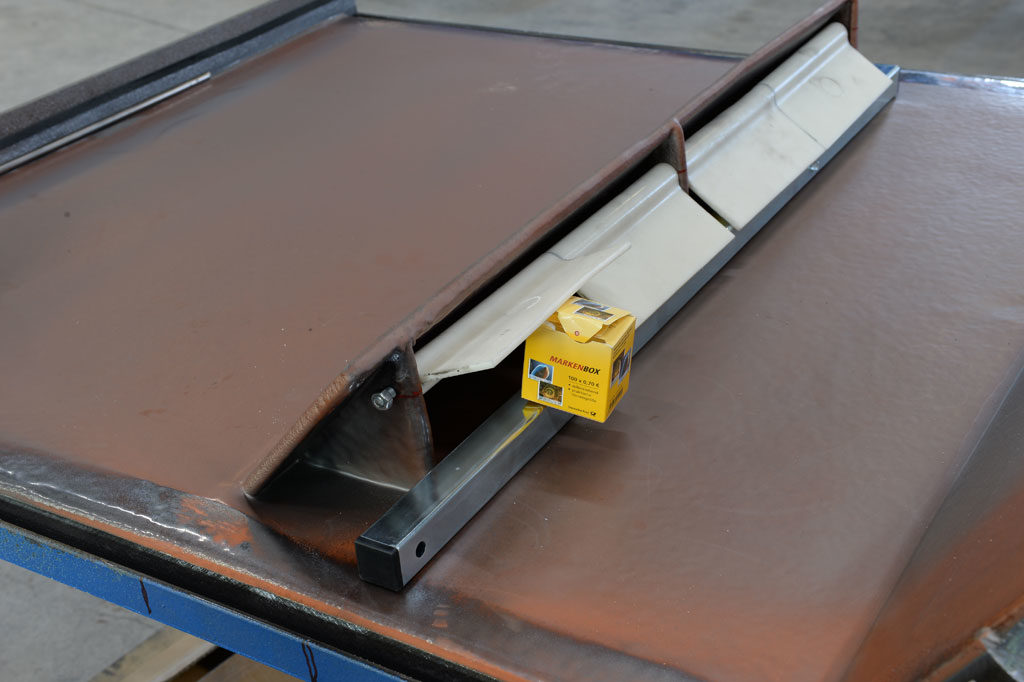
Um das zu überprüfen muss ich aber noch mal reinklettern in die Maschine und die Tür schließen lassen. In diesem Fall werde ich versuchen ein besseres Foto von innen zu machen, – dann mit montierten Dichtlippen. Außerdem warte ich jetzt sehnsüchtig auf den nächsten Auftrag mit den kleinen leichten Bauteilen…
Zum Abschluss des Projektes noch eine Aufnahme aus dem Inneren der Muldenbandstrahlanlage bei geschlossener Tür. Ich habe dazu eine Kamera mit Weitwinkelobjektiv und Selbstauslöser mit Hilfe eines umgebauten Statives auf das Muldenband gestellt. Belichtet wurde mit einem LED-Lichtpanel.
Auf diesem Bild ist jetzt auch der oben erwähnte Spalt zwischen der Unterkante der Prallplatte und dem gelochten Gummiband sehr gut zu erkennen.
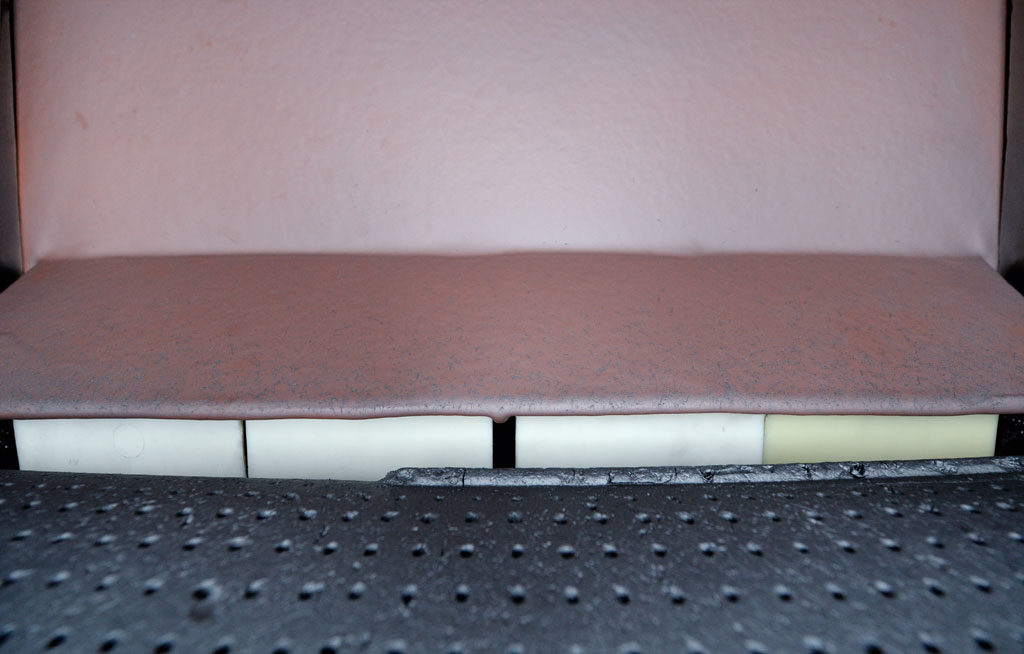
Wenn sich das Muldenband bewegt, so würde es im Normalbetrieb auf den Betrachter zulaufen. Die Unterkanten der vier Dichtlippen würden ein Stück in Richtung Kamera mitlaufen und dabei umklappen. Aber die Kamera würde dann umfallen. Deshalb gibt es davon kein Bild…
Die Dichtlippe auf der rechten Seite ist übrigens aus einem Polyurethan eines anderen Herstellers gegossen. Das Produkt läuft unter dem Namen Vytaflex 60. Es hat eine deutlich längere Topfzeit als das Elastocoat C 6905, ist aber auch dickflüssiger und benötigt daher etwas mehr Geduld beim Mischen und Gießen. Ich wollte einmal sehen ob sich ein anderes Verschleißverhalten zeigt.
13.12.2016 Jetzt wäre ich nicht der Sinning, wenn ich es dabei belassen könnte. Es hat mir am Ende doch keine Ruhe gelassen. Ich wollte sehen wie sich die Dichtlippen bei laufender Maschine verhalten. Aber selber drin sitzen und filmen war mir dann doch eine Nummer zu spektakulär. Also schnell ein neues Sonderstativ in die Muldenbandanlage eingeschweißt, ein LED-Panel und die D4 mit Weitwinkelobjektiv montiert und eine Videoaufnahme bei laufendem Band erstellt.
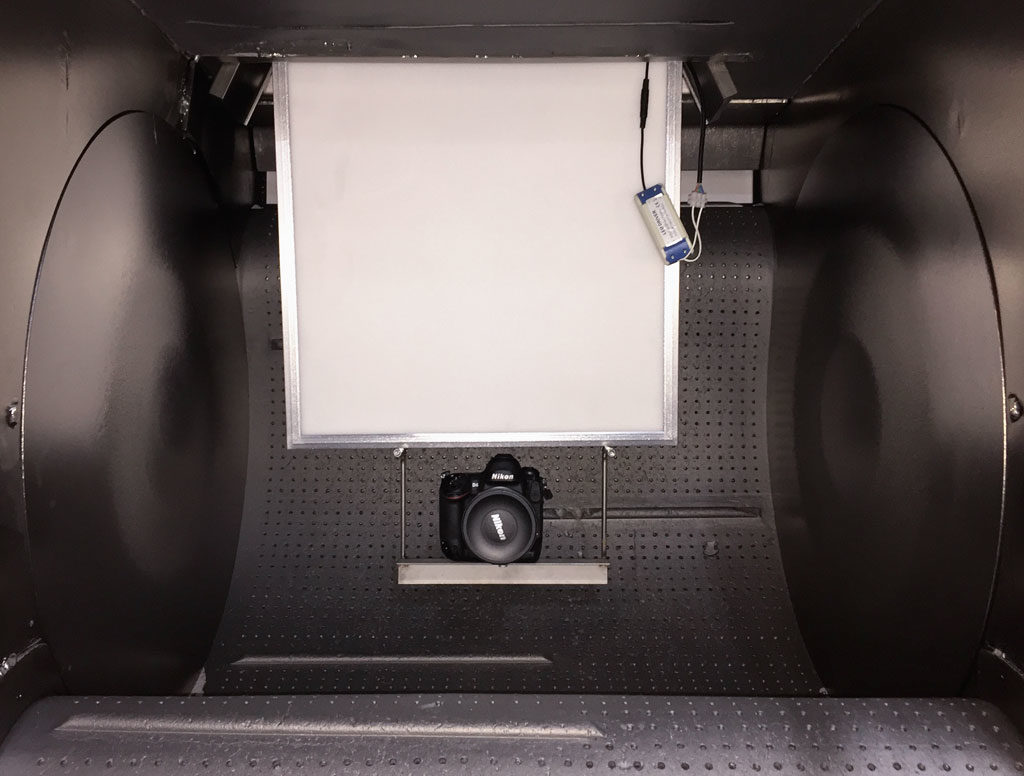
Jetzt sieht man auch sehr schön, wie die versetzten Stollen die Dichtlippen mitnehmen und in die richtige Lage bringen. Schade, dass ich nicht auch noch beim Strahlen zuschauen kann. Aber wer weiß schon, was die Zukunft noch so bringt…
Ein Gedanke zu „Muldenband-Strahlanlage abdichten“