Bau eines Carbon Front-Fenders
30.10.2018 Ein langer Winter mit wenigen Sonnenstunden steht vor der Tür.
Ich möchte mich gern an den Bau eines Front-Fenders aus Carbon für meine Husqvarna 701 Supermoto wagen.
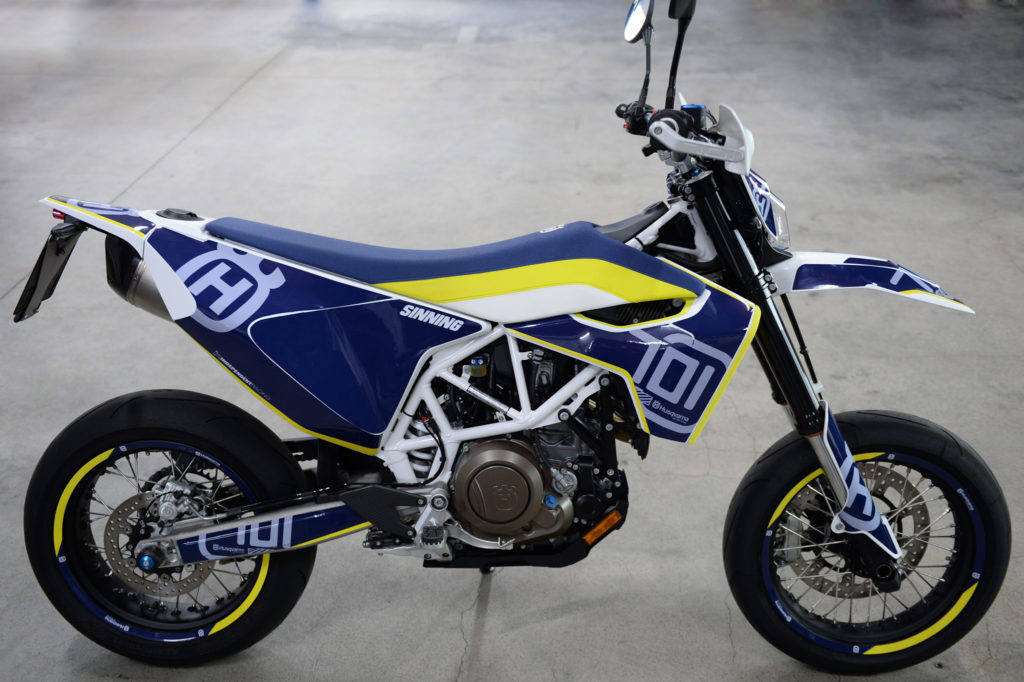
So sieht der Serienkotflügel im demontierten Zustand aus:
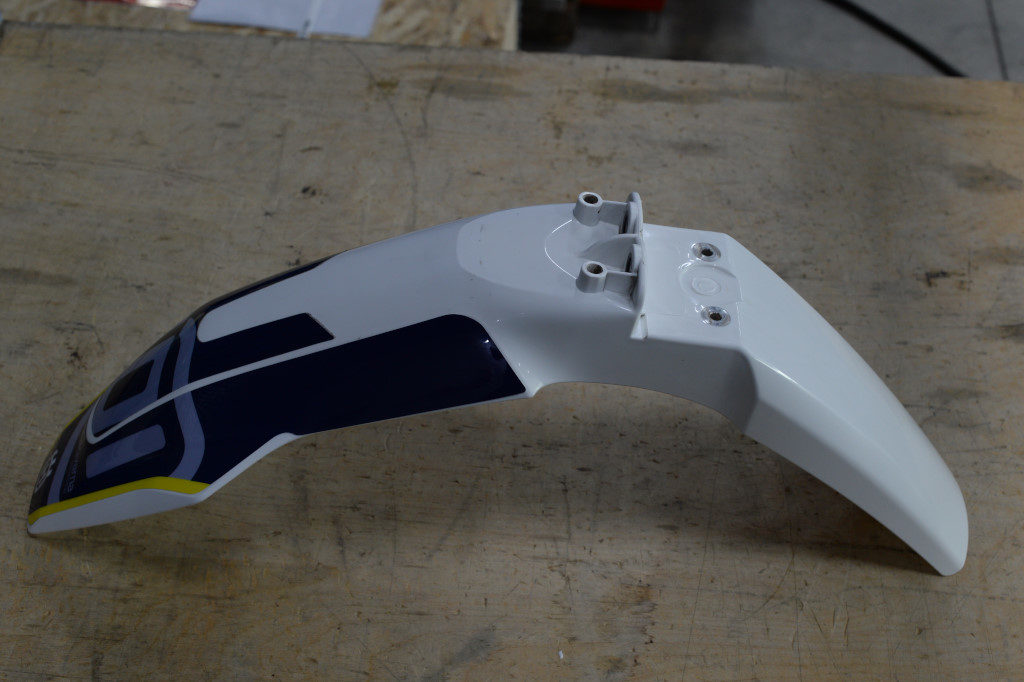
Wären die Befestigungspunkte nicht so komplex ausgeführt, so ließe sich ein Carbonteil in einer einteiligen Form herstellen. Das Originalteil besteht noch dazu aus Polypropylen und ist schön glatt unter dem Dekor. Das gäbe eine spiegelglatte Carbon-Sichtfläche. Aber der Bereich der Befestigungen ist als Spritzgussteil konstruiert und so nicht ohne größeren Aufwand abformbar.
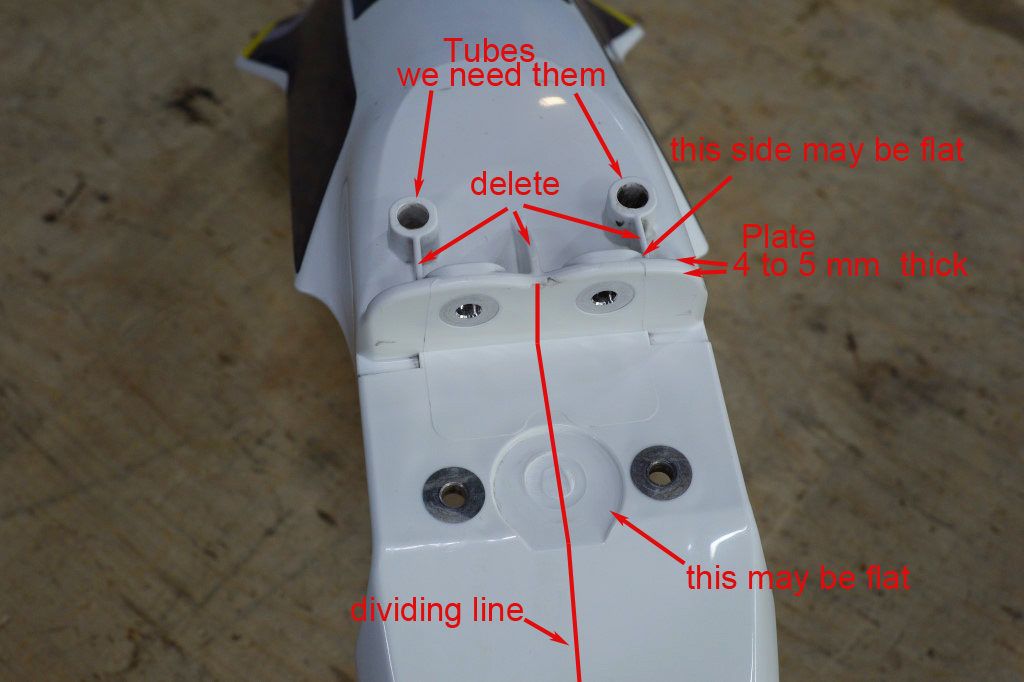
Hier muss umkonstruiert werden, um das Teil aus Faserverbundwerkstoffen zu fertigen.
Ich muss erst ein Originalteil besorgen, vermessen, modifizieren und für das Abformen vorbereiten. Außerdem muss der Winkel der seitlichen Wände im mittleren Teil gemessen und ggf. korrigiert werden, weil sich parallele Wände oder Hinterschnitte schlecht entformen lassen.
Das kriegen Sie nicht hin
30.10.2018 Ich habe ein in Deutschland ansässiges Unternehmen, welches sich mit Faserverbundwerkstoffen beschäftigt, per Mail um Unterstützung und Rückruf gebeten. Telefonisch riet man mir jedoch vom Nachbau ab. Man sieht nur Probleme, kann aber keine Lösungen bieten.
„Das kriegen Sie nicht hin…“ sagt man mir am Telefon.
Hier rufe ich nicht mehr an!
(Schade um den schönen Umsatz)
Ich werde es natürlich trotzdem versuchen.
Irgendwie gefällt mir das sogar, wenn die Experten sagen „Das geht nicht“ und ich es dann trotzdem hinbekomme. Aber so weit ist es noch nicht.
Jetzt stehe ich jetzt per Mail mit EasyComposites aus England in Verbindung. Die haben übrigens auch recht gute Videos auf Youtube. Ab jetzt läuft die gesamte Kommunikation auf Englisch. Englische Fachterminologie – das hatte ich mir anders vorgestellt.
Nebenbei bemerkt kosten die meisten Sachen in England ungefähr die Hälfte von dem, was ich in Deutschland hätte bezahlen müssen. Da kann man dann auch gleich ein bisschen mehr bestellen…
Jetzt muss ich mir einen originalen Kotflügel besorgen und diesen modifizieren. Meinen Eigenen möchte ich dazu nicht benutzen. Ich möchte die 701 im fahrbereiten Zustand. Falls das Wetter mal unerwartet schön wird.
01.11.2018 35 Minuten Telefongespräch mit England. Mein Gesprächspartner spricht sehr undeutlich und schnell. Er ist für mich nur sehr schwer zu verstehen. Ein paar hilfreiche Tipps bleiben aber doch hängen. Außerdem gibt es eine Menge „Starter-Kits“. z.B.:
Uni-Mould Complete Mould making Kit
Mit diesem Kit lässt sich eine Form erstellen. Eigentlich wollte ich den „Uni-Mould Complete Mould making Kit“ auch bestellen. Dieser besteht aus:
Regular Kit (0.7sqm) | Large Kit (3.3sqm) | |
---|---|---|
Estimated Mould Area | 0.7sqm | 3.3sqm |
Uni-Mould Tooling Gelcoat | 1kg | 5kg |
Uni-Mould Coupling Coat | 1kg | 5kg |
Uni-Mould Tooling Resin | 5kg | 25kg |
100g Chopped Strand Mat | 2sqm | 7sqm |
450g Chopped Strand Mat | 2kg | 7kg |
MEKP Catalyst (MAINLAND UK ONLY) | 200ml | 1L |
Plastic Finned Laminating Roller | 50mm Width | 75mm Width |
Laminating Brush | 2x 2″ | 2x 3″ |
Nitrile Gloves | 10 pairs | 10 pairs |
Aber: MEKP wird nicht verschickt. Also muss ich, zumindest einen Teil der benötigten Sachen, doch bei deutschen Händlern kaufen.
Für die Herstellung des ersten Carbonteiles gibt es dann wieder verschiedene Kits:
Carbon Fibre Laminating Starter Kit
Dies ist ein Kit für das Laminieren von Carbonfasern von Hand und er enthält:
- 0.3sqm 2/2 Twill 3k Carbon Fibre Cloth
- 385g EL2 Laminating Epoxy Resin
- 115g AT30 FAST Epoxy Hardener
- 35ml PVA Mould Release Agent
- 2 pairs Nitrile Gloves, 2 Mixing Pots, 2 Mixing Sticks
Es gibt ihn in zwei Varianten: „regular“ und „high temperature“.
Vacuum Bagging Starter Kit
Mit dem „Vacuum Bagging Starter Kit“ lässt sich ein von Hand laminiertes Bauteil im Vakuum aushärten. Dieser enthält:
- TBC2 Through-Bag Connector with ¼-turn valve and hose-tail barb fitting
- 5m 6mm ID PVC Vacuum Hose
- 5m VB160 Vacuum Bagging Film (1.52m wide)
- 5m PP180 Peel Ply (Abreißgewebe)
- 5m R120-P3 Perforated Release Film (Lochfolie)
- 2x 15m Gum Sealant Tape
- 5m BR180 Breather Layer Cloth
- 8 Pairs of Nitrile gloves
Resin Infusion Starter Kit
Mit dem „Resin Infusion Starter Kit“ lassen sich Bauteile herstellen, bei denen die Carbonfaser über ein Vakuum mit Harz getränkt werden. Das Resin Infusion Starter Kit enthält „IN2 Epoxy Infusion Resin 1kg Pack SLOW“ Harz.
- 1x Professional Resin Catch Pot with vacuum gauge and liners
- 2x Infusion Tube Line Clamp
- 2x Silicone Resin Infusion Connector
- 5m 6mm ID PVC Vacuum Hose
- 5m VB160 Vacuum Bagging Film (1.52m wide)
- 5m PP180 Peel-Ply
- 5m FM100 Resin Infusion Mesh
- 10m Resin Feed Spiral
- 2x 15m Roll Vacuum Bagging Sealant Tape
Für Handlaminat wird jedoch „EL2 Epoxy Laminating Resin 500g SLOW“ empfohlen.
Ich habe dann auch gleich meine erste Bestellung nach England abgeschickt. Alle hier erwähnten Kits und noch ein paar Sachen mehr – eine lange Liste…
02.11.2018 EasyComposites darf kein MEKP verschicken und Kohlefaserhexel gibt es dort nicht. Also habe ich diese Sachen in Deutschland bestellt. Hier heißen die Kohlefaserschnitzel. Da muss ich sofort an meine Kochkünste denken.
Hierzu sind die Versandbenachrichtigungen auch schon raus. Die aus England übrigens auch. Die Zustellung aus England ist für den 06.11.2018 geplant. Das wird spannend…
Ich habe allerdings bisher noch keinen originalen Front-Fender auftreiben können. Mal sehen was der kommende Samstag bringt.
03.11.2018 Ein Anruf beim Händler meines Vertrauens ergibt: knapp 2 Wochen Lieferzeit auf den Original-Front Fender. Bei anderen Händlern sieht es derzeit nicht besser aus. Das geht ja schon mal gut los.
Warum baue ich selbst?
Da ich mit dem Formenbau noch nicht beginnen kann, möchte ich kurz darauf eingehen, warum ich das Ganze überhaupt anfange.
Ich habe schon öfter Carbonteile bestellt. Einige habe ich sofort wieder zurückgeschickt, andere musste ich umbauen, damit sie wenigstens halbwegs anständig montierbar waren.
Mit keinem dieser Teile war ich zu 100 % zufrieden. Die Qualität der Sichtseite ist in den meisten Fällen sehr ordentlich. Was mir häufig nicht gefällt, sind die Passform und die Ausführung der Verschraubungspunkte.
Fakt ist, dass die Wandstärken der Carbonteile an den Verschraubungspunkten häufig zu dünn ausgeführt sind und die Teile sich um die Schraube herum bewegen können.
Und dann versucht mir ein Händler beispielsweise zu erklären, dass ein 270,- € teures Carbonteil nun mal Rappelt. Das läge am Carbon sagt der. Nein, liegt es nicht!
Ich möchte mal ein Beispiel bringen:
In der Vergangenheit hatte ich ein Paar Gabelabdeckungen und ein Paar Versenschützer aus mattem Carbon bestellt. Die Teile sehen alle sehr hochwertig aus, allerdings passten die nicht so besonders gut und die Verbindungs- /Verschraubungspunkte waren nicht sauber durchdacht.
Heel Guards
Beide Versenschützer hatten z.B. zu kleine Bohrungen. Die originalen Schrauben haben einen Durchmesser von 8 mm. Die Löcher im Versenschützer waren gerade mal 6,5 mm im Durchmesser. Zu der Zeit dachte ich noch, dass sei das einzige Problem und habe mit einer Diamant-Rundfeile die Löcher vorsichtig so weit vergrößert, dass die originalen Schrauben durchpassten.
Nachdem ich die Versenschützer nun festschrauben konnte, musste ich feststellen, dass der linke Versenschutz im falschen Winkel anliegt und nur 2 mm weit von der hängenden Schwinge absteht. (Das Motorrad stand aufgebockt) Wenn die Schwinge jetzt noch einfedert und die Verse einen leichten Druck ausübt, so gibt es möglicherweise Kratzer in der Schwinge.
Also habe ich die angeschliffene Auflagefläche um die Bohrung herum auf der Rückseite der Versenschützer mit feinem Schleifpapier ganz leicht im Winkel korrigiert und jeweils eine Karosseriescheibe dahinter montiert. Jetzt passt der Abstand zur Schwinge so gerade eben. Allerdings drückt die Schraube an dieser Stelle nur gegen 0,5 bis 1 mm Materialstärke Carbon. Für mich ist das eine Sollbruchstelle. Weil ich die Versenschützer bearbeitet habe, kann ich die jetzt auch nicht mehr zurückschicken.
Hier hätte man z.B. bei der Herstellung ein paar zusätzliche Lagen Carbon um die Verschraubungspunkte aufbringen können. Ein paar 3 bis 4 cm große, runde Stücke hätten so gut wie nichts gekostet, so gut wie nichts gewogen, dafür wäre aber unter den Schrauben genügend Futter zum Einleiten der Kräfte in das Bauteil und für die Korrektur des Winkels.
Front-Fork-Covers
Bei den Front-Fork-Covers sah es nicht viel anders aus.
Auch hier müsste man die Bohrungsdurchmesser an die Schrauben anpassen. Die Originalschrauben sind M 6 – Schrauben mit dickerem Schaft. Der Schaft dient dazu, zu hohe Presskräfte durch den Schraubenkopf am Kunststoffteil zu verhindern.
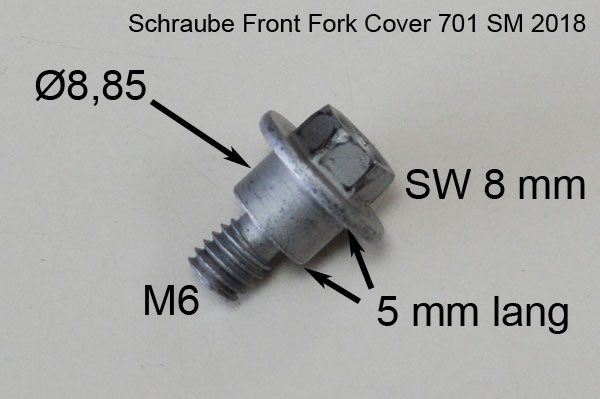
Bei den wesentlich dünneren Carbonteilen ist dann nach dem Festschrauben noch ca. 4mm Luft unter dem Schraubenkopf und das Carbonteil hat entsprechend viel Spiel. So montiert neigen Carbonteile zu starken und lauten Vibrationen. Hier hätte man grundsätzlich ein paar Kunststoffscheiben beilegen können.
Der rechte Gabelschützer hatte nach der Montage auf der inneren Seite Kontakt zum äußeren Gabelrohr. Das hätte auf Dauer beim Einfedern zu einer blanken Stelle am äußeren Gabelrohr geführt.
Der linke Gabelschützer hätte zum äußeren Gabelrohr zwar keinen Kontakt gehabt, aber die Klemmung des Kabels für das Tachosignal und die Bremsleitung sind zu eng ausgeführt. Die 2018er 701 SM hat um die Bremsleitung herum extra einen Metallring, welcher im originalen Gabelschützer genau geführt wird.
Ich finde Carbonteile am Motorrad äußerst sexy, aber ich lege genau so viel Wert auf eine anständige Passform und auf sichere Verschraubungen. Außerdem möchte ich keine schnarrenden Verkleidungsteile an meinem Motorrad. Ich hätte kein gutes Gefühl wenn sich die Montage schon nicht vernünftig durchführen lässt.
Ich hoffe, dass ich einige, vielleicht sogar alle diese Fehler an meinem Front-Fender vermeiden kann. Wir werden sehen.
Formbau – Es geht los!
06.11.2018 Kleines Weihnachten: alle Pakete sind eingetroffen. Nur der Kotflügel fehlt leider noch. Und weil ich es mit der Geduld nicht so habe, habe ich gleich an mehreren Stellen einen Kotflügel bestellt. So teuer sind die schließlich nicht. Das erhöht die Chancen auf eine schnelle Lieferung. Man muss auch bereit sein, für ambitionierte Projekte Opfer zu bringen.
08.11.2018 Der erste Kotflügel ist heute eingetroffen. Bevor ich es jetzt vergesse, wird er, für den späteren Gewichtsvergleich, erst einmal gewogen. 470 Gramm bringt der auf die Waage. Nicht dass es mir bei diesem Projekt um das Bauteilgewicht geht, aber man möchte ja schon so ungefähr wissen wo die Reise hingeht.
Jetzt liegt das Ding vor mir und ich mache mir Gedanken über die Anordnung der Trennkanten.
Wären die Verbindungselemente, also die beiden Rohrabschnitte (1) und die Platte (2) nicht, so könnte man fast mit einer einteiligen Form arbeiten. Leider werden diese Verbindungselemente für die Fixierung des Scheinwerfers und die Montage des Front-Fenders an der unteren Gabelbrücke benötigt.
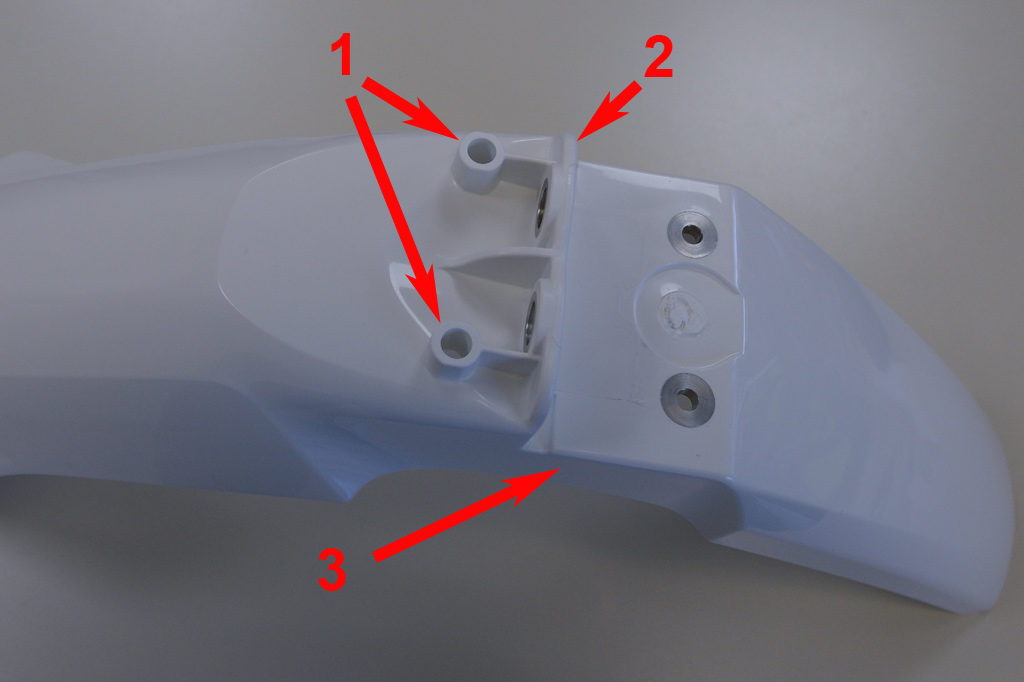
Außerdem sprechen die beiden parallel zueinander stehenden Wände (3) gegen eine einteilige Form.
Ein Vorschlag des Supportmitarbeiters von EasyComposites war, den Kotflügel zunächst in einer einteiligen Form herzustellen und die Verbindungselemente später anzukleben. Aber ich traue einer Klebeverbindung in diesem Fall und insbesondere an einem Einzylinder-Motorrad nicht so weit über den Weg. Ich möchte lieber einen durchgehenden Faserverlauf in die Platte hinein und wieder heraus. Außerdem muss, im Falle einer Klebeverbindung, das angeklebte Bauteil beim Kleben sehr genau ausgerichtet werden, damit später alles passt. Ich behalte mir diese Option aber mal vor, falls mein Weg sich als nicht so glücklich erweisen sollte.
09.11.2018 Aus Bastelkarton mit einem Flächengewicht von 380 g/m² habe ich heute (Quick and dirty) eine Trennkante mit Heißkleber an das Bauteil geklebt. Die vordere Hälfte lässt sich meiner Meinung nach relativ unproblematisch aus einen Stück fertigen. Die Trennlinie zum hinteren Teil des Kotflügels verläuft somit fast unsichtbar entlang der äußeren Gabelrohre.
Die Trennkanten aus Bastelkarton habe ich mit Heißkleber fixiert. Für die Trennflächen aus Bastelkarton wollte ich AFH-1 Trennmittel verwenden. Das hatte ich von anderen PU-Projekten aus der Vergangenheit noch hier. Es handelt sich hierbei um ein Wachsgemisch mit Lösemitteln und es lässt sich mit dem Pinsel relativ leicht auftragen. Für den Kotflügel werde ich Easy-Lease als Trennmittel verwenden.
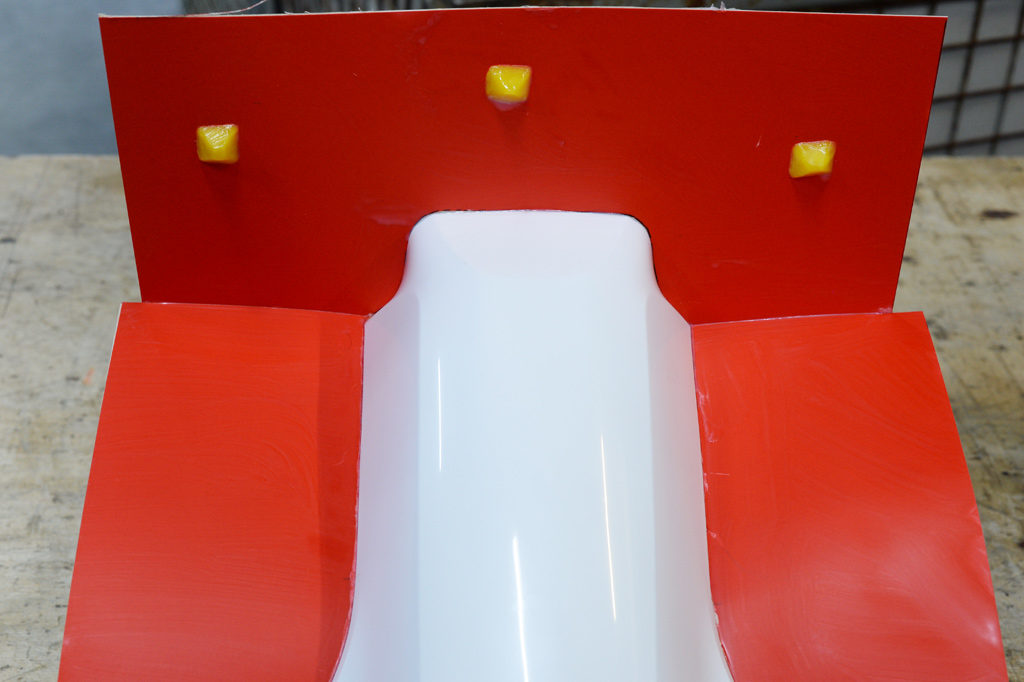
Leider zeigt sich kurze Zeit später, dass das AFH-1 Trennmittel die Pappe durchdringt und auch auf der Rückseite einen wunderbaren Job macht. Die Pappe löst sich vom Heißkleber ab.
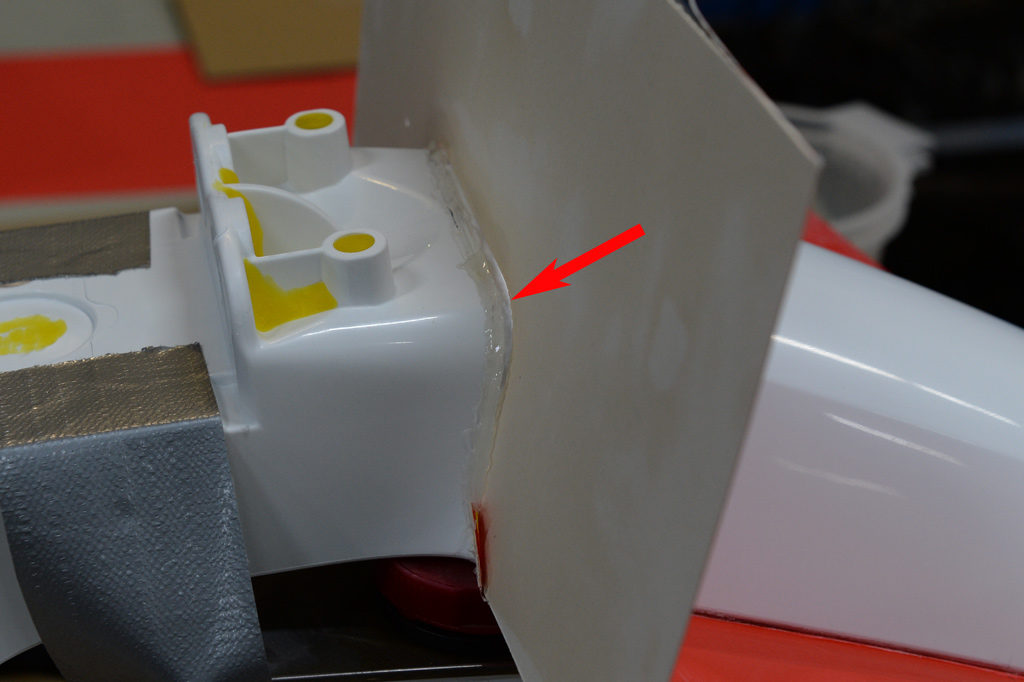
Auf diese, teilweise abgelöste Trennkante kann ich jetzt aber kein Formbau-Feinschichtharz (Tooling Gel Coat) auftragen. Das würde mir vermutlich auseinanderfallen. Heute (Samstag) werde ich auf die Schnelle wohl auch kein Ersatzmaterial mehr bekommen. Immerhin reichen die Zeit und das vorhandene Material um ein Hilfsgestell zu bauen.

Alles für die Katz: jetzt muss ich irgendwo ein anderes Material für die Trennkanten auftreiben.
11.11.2018 Ich habe einen zweiten, trotzigen Versuch mit der Bastelpappe unternommen. Diesmal habe ich nur eine Schicht AFH-1 Trennmittel aufgetragen.
Als auch eine Stunde nach dem Trocknen des Trennmittels die Pappe immer noch fest am Kotflügel hing, war ich mutig genug für die erste Lage Formbaufeinschicht.
Also habe ich, bei einer Raumtemperatur von 20,0 Grad Celsius, 100 g Formbaufeinschicht (Tooling Gel Coat) mit ca. 1,75 % MEKP Härter angesetzt und vorsichtig auf Kotflügel und Pappe gepinselt. Jetzt muss das Ganze ca. 2 bis 3 Stunden anhärten, bevor ich die zweite Lage auftragen kann.
20:00 Uhr: die zweite Lage ist drauf. Was für ein Gestank…
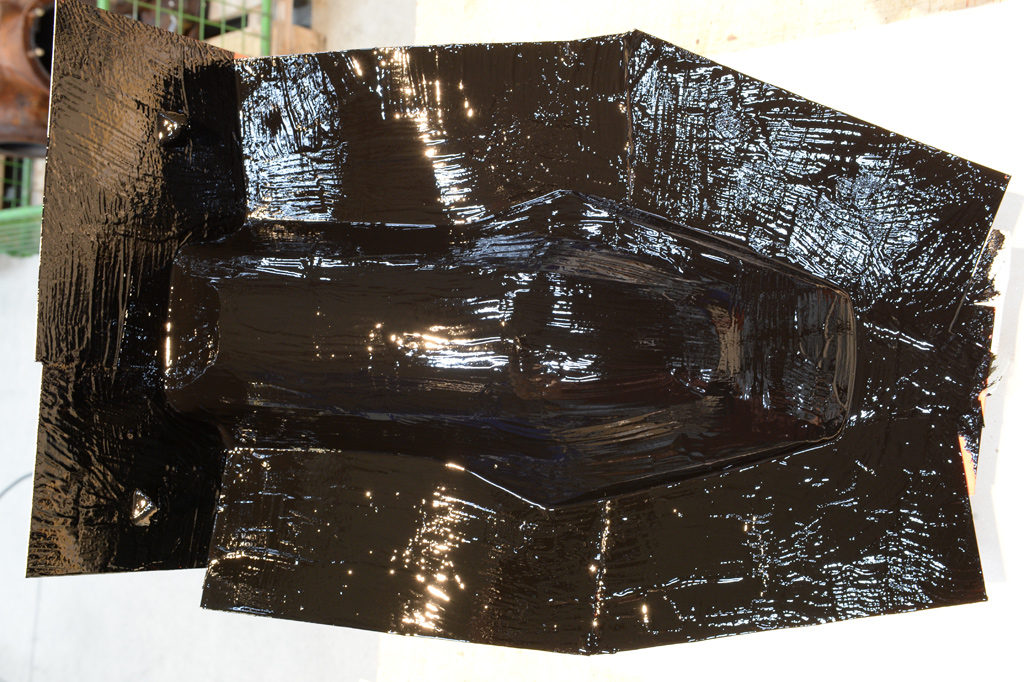
12.11.2018 Vor Arbeitsbeginn schnell die Kupplungsschicht (Coupling-Coat) mit 2 Lagen zu je 100 g/m² emulsionsgebundener Glasfasermatte (Chopped Strand Mat – Emulsion Bound) aufgelegt. Ich habe für den knapp ¼ m² großen Bereich der Form 200 g Harz mit etwas über 1,5 % MEKP (etwa 3 g) angesetzt.
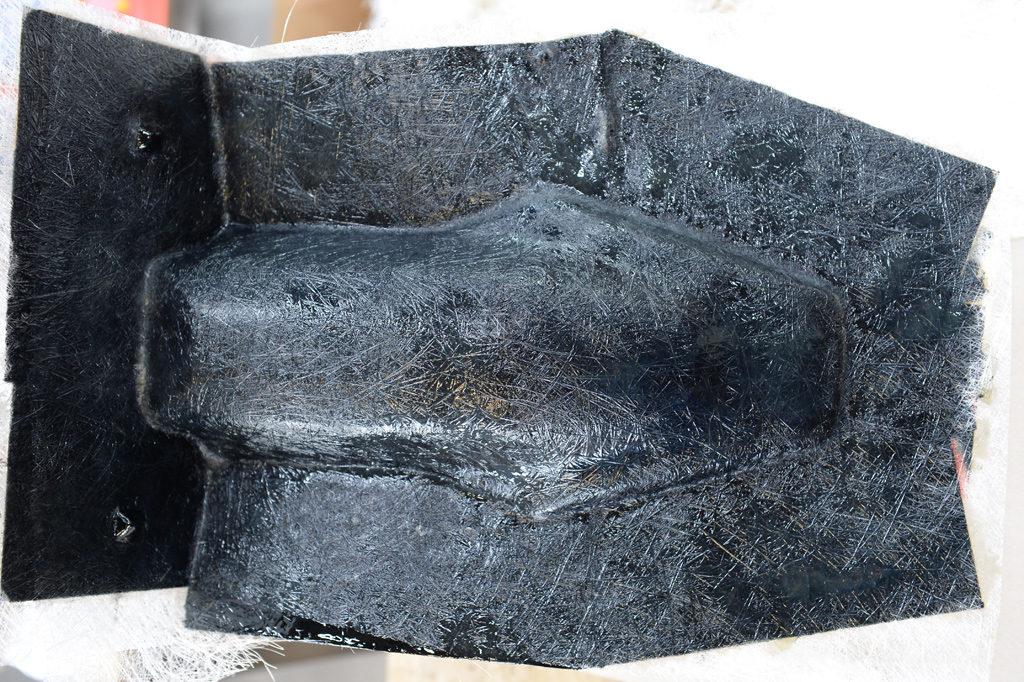
Bei einer Raumtemperatur von 20,0 Grad Celsius kommt hier schon Hektik auf. Die Topfzeit beträgt bei diesem Mischungsverhältnis gerade mal rund 20 Minuten. Der Rest geliert schon im Mixbecher, während ich noch die letzten Fasern antupfe.
Die Mittagspause nutze ich zum Aufbringen der letzten 4 Lagen Glasfasermatte mit einem jeweiligen Flächengewicht von 450 g/m². Ich setze für jede Lage 500 g Harz mit 0,8 % MEKP an. Das verschafft mir ein bisschen mehr Zeit. Zulässig für das Formbau-Harz (Tooling Resin) sind 0,75 bis 1,25 % MEKP.
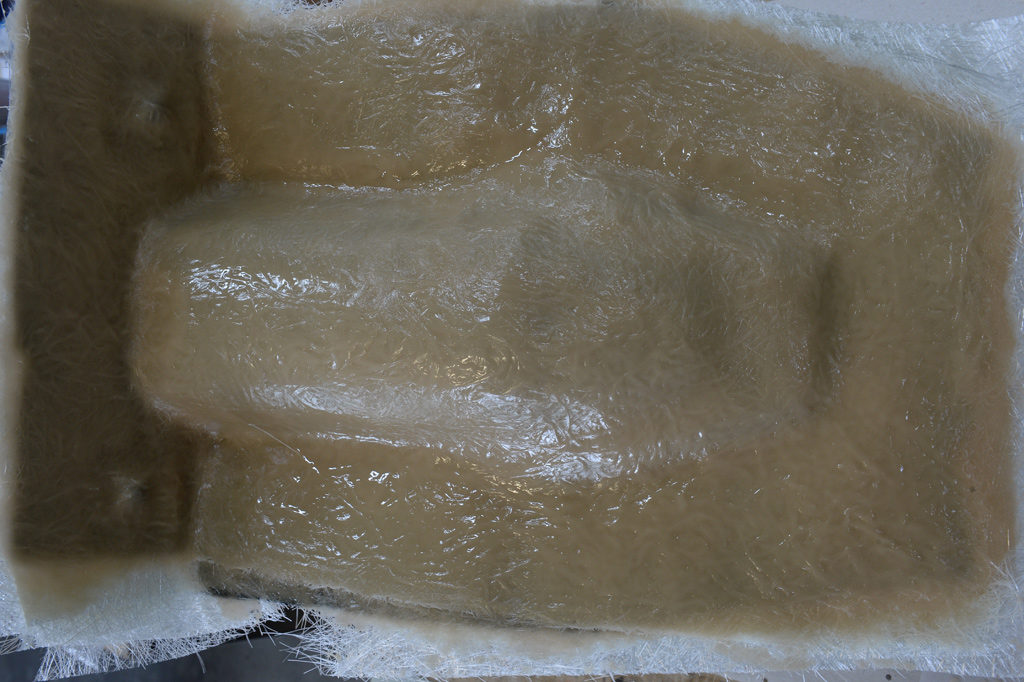
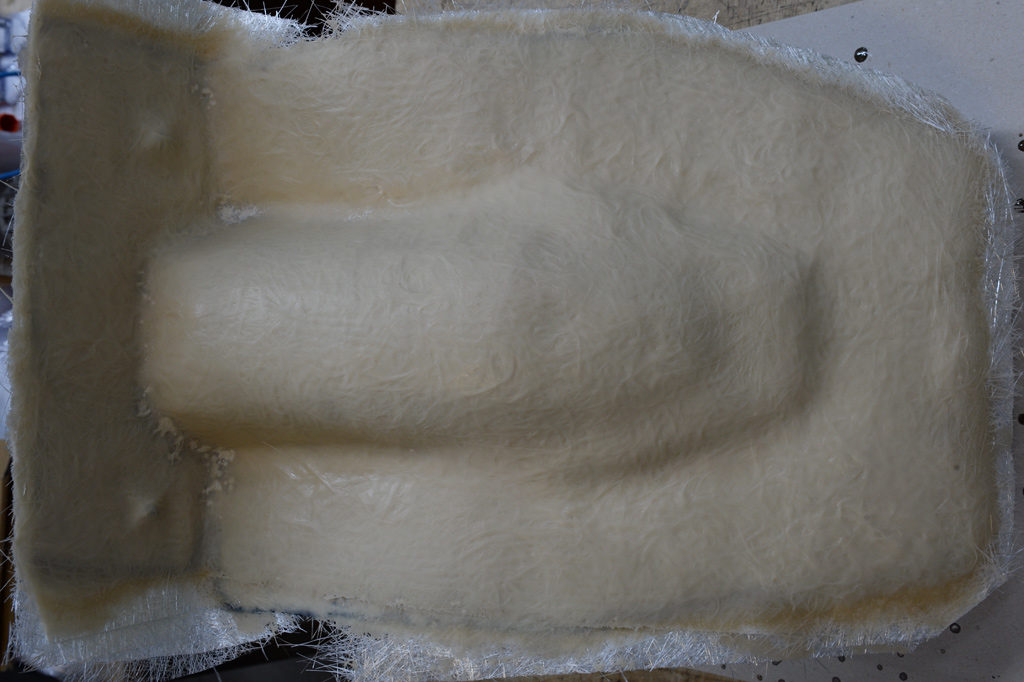
Resümee des Tages:
Die Harze riechen sehr stark! Der Geruch begleitet uns noch während der nächsten zwei Tage und das, obwohl die Halle eine Grundfläche von 625 m² hat und über 6 m hoch ist. Ich habe die Idee, Carbon Teile zu bauen, heute mehrfach bereut.
Bastelpappe für die Flansche zu verwenden war auch nicht mein bester Einfall. Hier muss was Stabileres her. Mit der kurzen Topfzeit im Nacken, muss man schon ordentlich auf die Tube drücken und den Pinsel fliegen lassen. Da bleibt keine Zeit für zartes Tupfen. Das Ganze wackelt beim laminieren wie ein Lämmerschwanz und ich habe die ganze Zeit die Sorge, dass mir alles auseinander fällt.
Ich glaube, dass es besser gewesen wäre, die Raumtemperatur und den prozentualen Anteil des Härters (MEKP) an der unteren zulässigen Grenze zu halten. Das hätte den Zeitdruck etwas reduziert.
Ein Anmischbecher mit etwas Aceton hätte auch nicht geschadet. Ich habe heute 6 Pinsel verbraucht.
Für meine Hände (Handschuhgröße 12) gibt es keine Nitril-Einmalhandschuhe zu kaufen. Die Mehrweghandschuhe sind viel zu steif und meine MaxiFlex-Arbeitshandschuhe schützen vor den Harzen nicht richtig.
Außerdem habe ich ein paar Lufteinschlüsse unter dem Harz. Sowohl im Coupling Coat, als auch im Toolig Resin. Der Zeitdruck war wohl ein bisschen zu hoch. Schlampig gearbeitet!
13.11.2018 Ich habe mit dem zweiten Teil der Form begonnen. Diesmal verwende ich die 2 mm starke Polypropylen-Platte, damit die Trennflächen etwas stabiler sind und beim Laminieren nicht so wackeln. 2 mm starkes PP lässt sich aber nicht mal eben mit der Schere zuschneiden. Aus Bastelkarton habe ich zunächst eine Schablone angefertigt, die der Bauteilkontur so exakt wie möglich folgt.
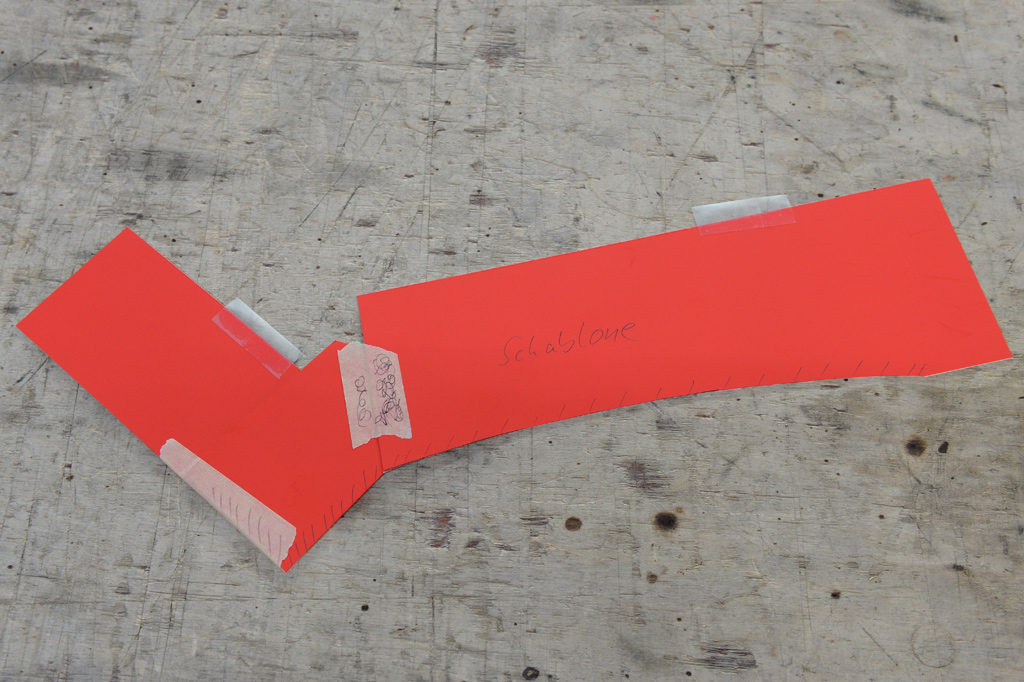
Die Kontur übertrage ich dann mit einem feinen Filzstift auf die PP-Platte. Am Frästisch und an der Bandsäge versuche ich dieser feinen Linie so genau wie möglich zu folgen. Das klappt auch recht gut. Die verbleibenden schmalen Spalte zum Bauteil muss ich dann später mit Wachs ausfüllen.
Inzwischen habe ich auch die rückseitige Pappe der vorderen Formhälfte entfernt. Das AFH-1 Trennmittel wirkt wunderbar, die Pappe lässt sich ganz leicht ablösen. Die Kante zum Bauteil ist sauber abgebildet, die beiden Indexpunkte sind auch schon vom Wachs befreit und die Reste vom Heißkleber entfernt. Der Heißkleber lässt sich übrigens mit Bremsenreiniger recht gut entfernen.
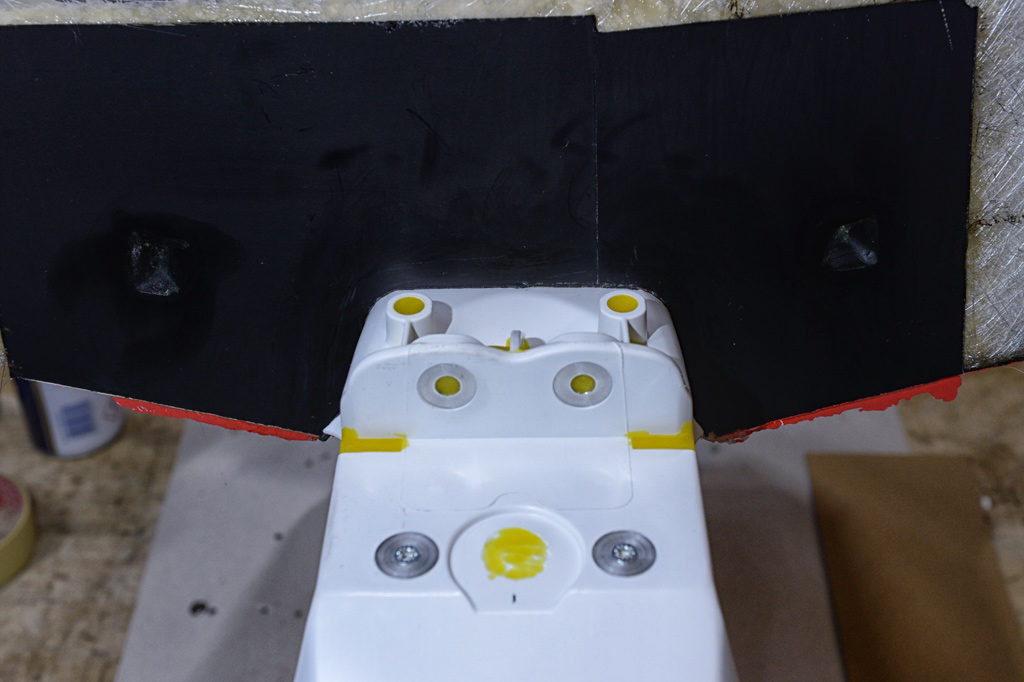
Ich werde den hinteren Teil des Front Fenders noch einmal der Länge nach teilen. Die Form wird also jetzt mindestens 3-teilig. Hierzu habe ich mit einem feinen Filzstift ein paar Striche entlang der Trennkante auf das Bauteil gezeichnet und die Trennfläche entlang dieser Linie angesetzt.
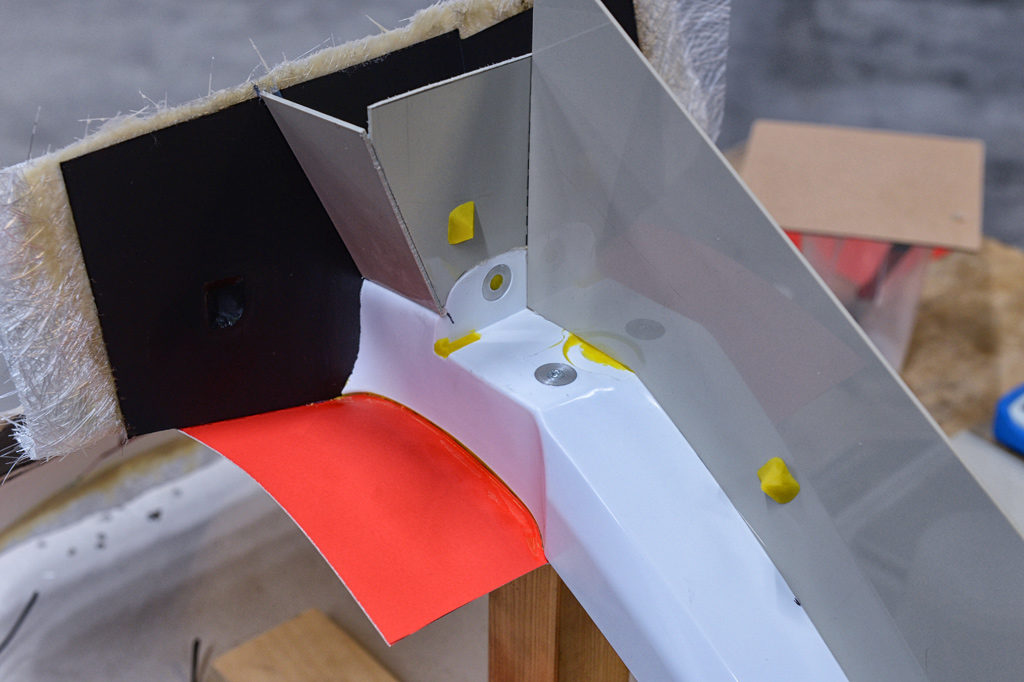
Die Formtrennwände aus stabilem Polypropylen passen. Ok, ein bisschen Bastelpappe ist auch wieder dabei; es hat ja doch recht gut geklappt beim letzten Mal. Für heute reicht es mir und es ist auch schon wieder nach 20:00 Uhr.
14.11.2018 Für die restlichen Flanschflächen muss heute wieder die Bastelpappe herhalten. Das zweite Formteil ist jetzt für die Formbaufeinschicht vorbereitet. Der Kotflügel ist mit „Easy-Lease“ Release Agent getrennt, die Flansche mit AFH-1. Die Fläche ist relativ klein und die 100 g Tooling Gel Coat auch schnell genug aufgepinselt. Ich setze den Gel Coat mit dem höchst zulässigen Härter-Anteil, also 2% MEKP an. Ich habe allerdings auf den starken Geruch keine Lust mehr und stelle die Form zum Aushärten bei laufender Absaugung über Nacht in den Strahlraum.
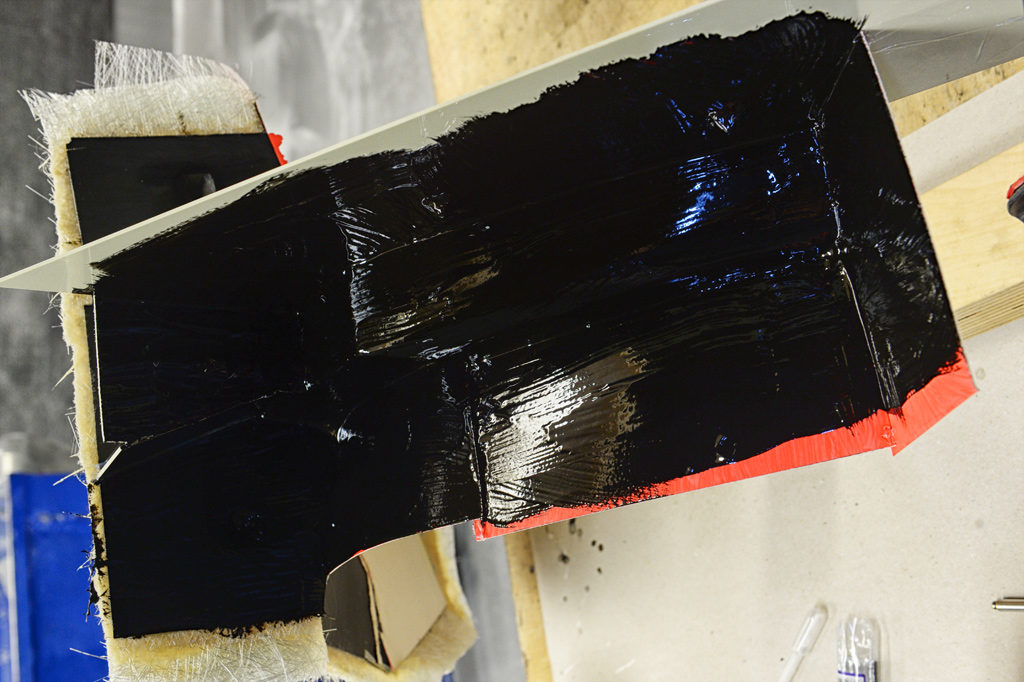
15.11.2018 Coupling Coat und 2 Lagen zu je 100g Chopped Strand Mat – Emulsion Bound konnte ich vor der Arbeit noch schnell aufpinseln. Tooling Resin und vier Lagen zu je 450g Chopped Strand Mat – Emulsion Bound kurz vor Feierabend ebenfalls.
Morgen früh kann ich mit dem letzten Formteil beginnen.
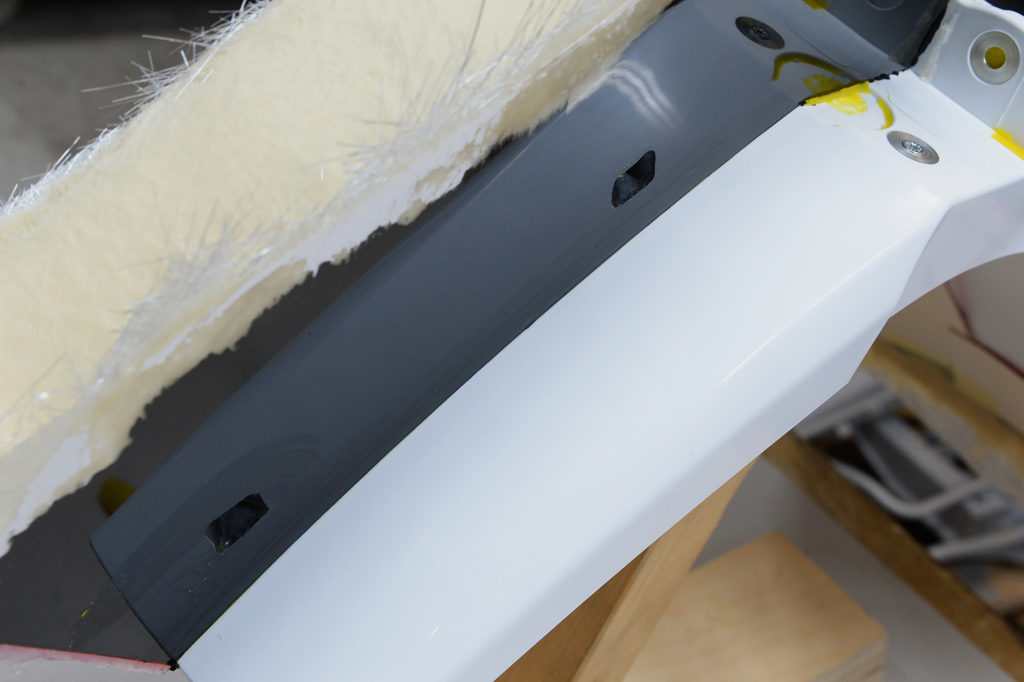
16.11.2018 Diese Trennkante gibt Hoffnung auf ein Gelingen des Projektes.
17.11.2018 Die üblichen Sachen sind jetzt auch am dritten Formteil passiert: Tooling Gel Coat, Coupling Coat mit 2 x 100 g/m² CSM und Tooling Resin mit 4 x 450 g/m² CSM.
Abends ist dann alles hart genug um schon mal vorsichtig ein paar Löcher zu bohren, um die Formteile miteinander verschrauben zu können. Die Ränder sind auch schon beschnitten und alles ist für den Guss des vierten Formteils vorbereitet.
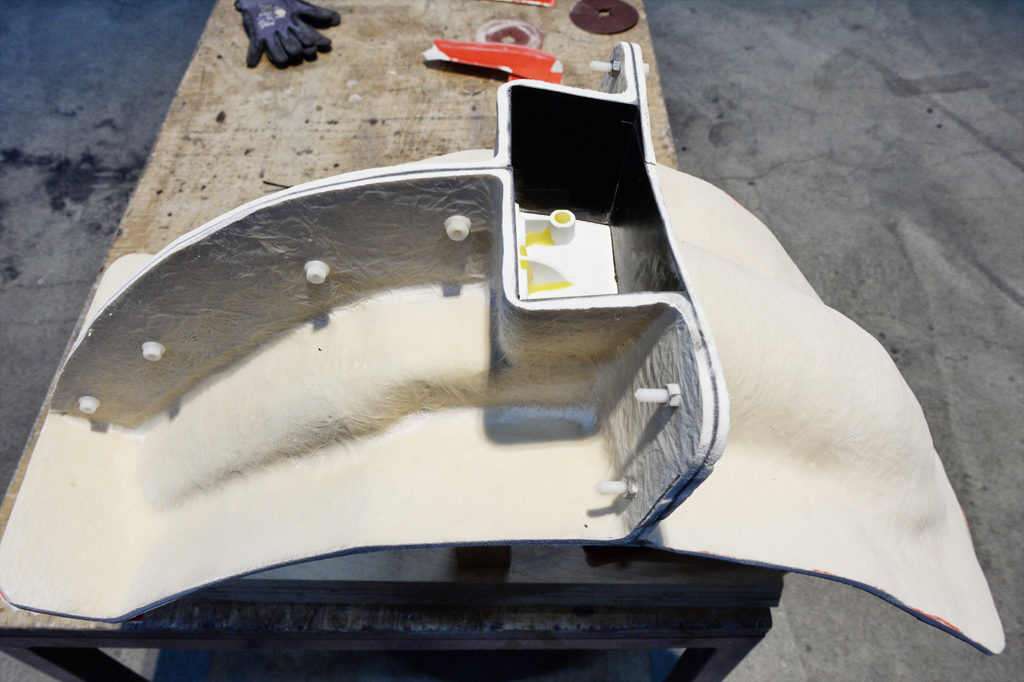
Ja, richtig gelesen: das vierte Formteil möchte ich aus Polyurethan gießen. Elastocoat C6905 von Vosschemie ist noch vorrätig. Dasselbe, was ich schon in verschiedenen Projekten wie „muldenband-strahlanlage-abdichten“ und „polyurethan-giessen“ benutzt habe. Die Komponenten sind schon über 2 ½ Jahre alt. Hoffentlich reagieren die noch anständig. Die B-Komponente, also der Härter, ist besonders empfindlich was das Altern angeht. Ich werde vorher eine Probe gießen müssen…
18.11.2018 Der Härter war noch ok, und das vierte Formteil ist ausgegossen. Ich habe die Innenseiten der Form vorher noch mit „Meguiar’s #8 Mirror Glaze Mould Release Wax“ getrennt. Jetzt könnte man noch über ein fünftes Formteil nachdenken um am vorderen Teil des Front Fenders noch die ersten paar Millimeter der Wölbung nach innen abzuformen. Das würde das spätere Carbonteil ein bisschen versteifen. Da schlafe ich jetzt mal eine Nacht drüber…
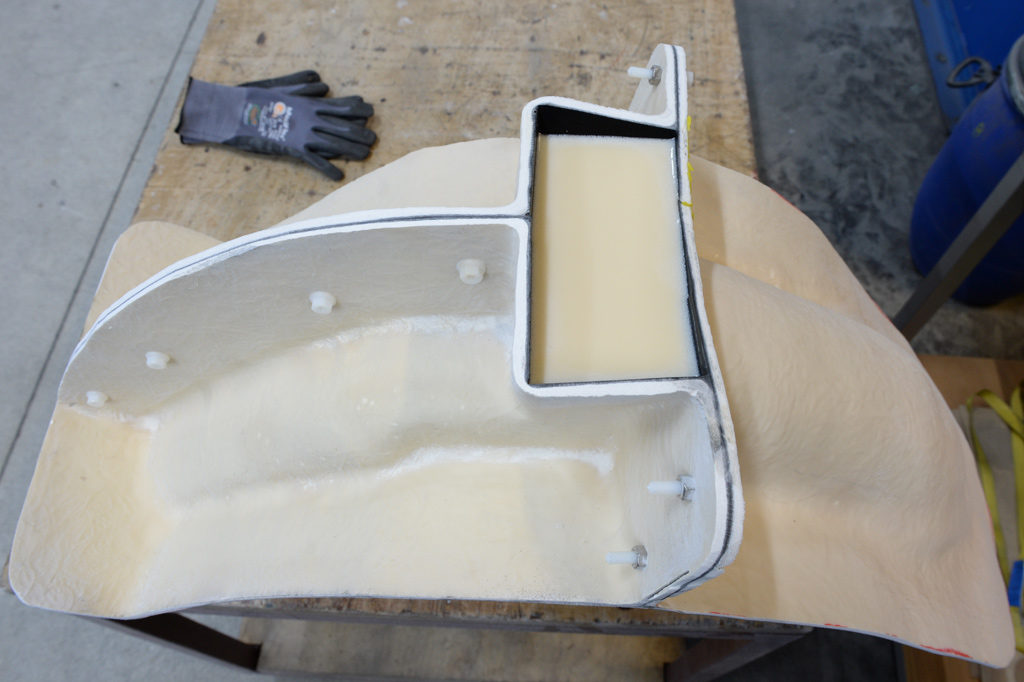
19.11.2018 Es wird kein fünftes Formteil geben – jedenfalls vorerst nicht.
Der PU-Guss ist inzwischen ausgehärtet und das Modell entformt. Jetzt zeigt sich, an welchen Stellen ich unsauber gearbeitet habe:
Es hat einige Fehlerstellen in den Flanschflächen gegeben (1), deren Ursachen mir nicht klar sind. Die werde ich wohl nacharbeiten müssen, falls ich mit dem Vakuuminjektionsverfahren arbeiten will.
Die Formflächen sehen jedoch alle sehr gut aus.
Außerdem habe ich im ersten Formteil, nachdem mir die Pappe abgefallen war, an der Grenzfläche zu den Befestigungselementen keine Schlösser mehr gesetzt. Diese Schlösser hätten aber das Formteil aus PU in Position gehalten. Jetzt sitzt das PU-Teil nicht klar definiert an einer festen Position, sondern ist ganz leicht beweglich. Das ist nicht gut und kann dazu führen, dass später im Carbon-Bauteil eine starke Kante sichtbar sein wird (2).
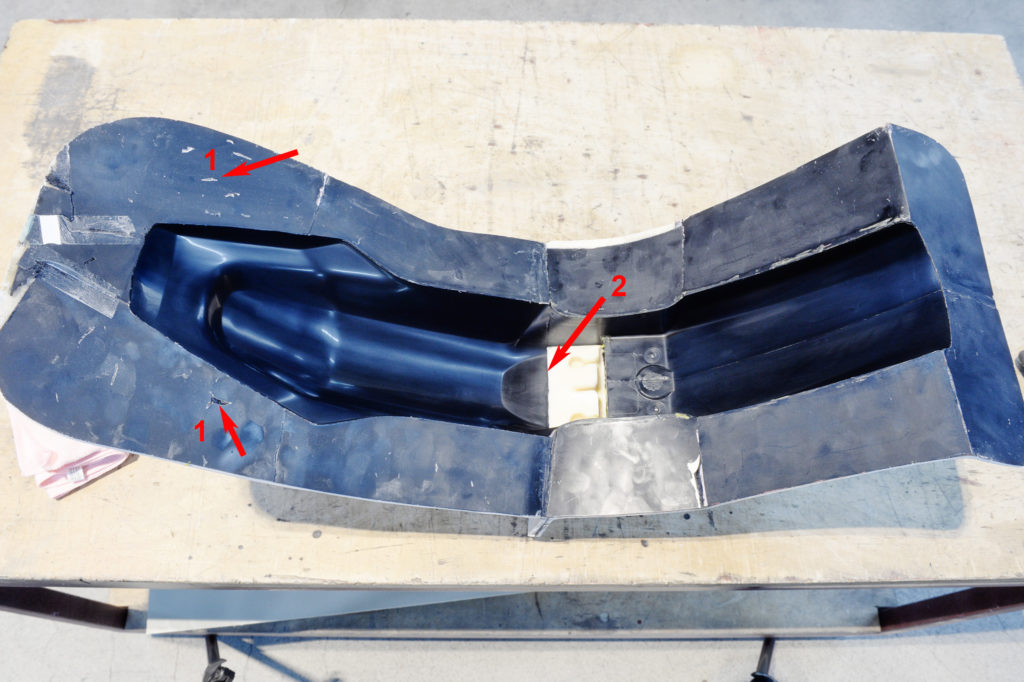
20.11.2018 Obwohl es mir jetzt unter den Nägeln brennt und ich am liebsten sofort mit dem Laminieren des ersten Carbonteiles anfangen möchte, muss leider zuerst die Form vorbereitet werden.
Außerdem muss ich mir noch eine Möglichkeit zur Fixierung des aus Polyurethan gegossenen vierten Formteils einfallen lassen. Diese Fixierung muss das PU-Formteil auch dann sicher in Position halten, wenn Vakuum ins Spiel kommt.
Dann muss ich mir darüber klar werden, welche der Befestigungselemente ich wirklich brauche und wie ich das technisch realisieren kann. Auf die beiden Röhren und auf die Anschraublippe kann und will ich nicht verzichten. Die schmalen Rippen dagegen könnten meinetwegen wegfallen.
Eine sehr einfache Möglichkeit wäre, „epoxy laminating resin“ mit Carbonfaserschnitzeln anzurühren und diese Masse vor dem Laminieren in die PU-Form zu spritzen. Das wäre vermutlich der einfachste Weg und möglicherweise ist das schon stabil genug.
Andererseits könnte man auch einen Streifen Carbongewebe zusammenrollen um damit die Röhren zu füllen. In den Spalt für die Lippe könnte ein Carbongewebe hineingefaltet werden. Dann muss man nur noch sehen, dass man das Harz hineinbekommt.
Ein paar zusätzliche Verschraubungspunkte sind dagegen schnell gesetzt.
Da das erste Carbonteil vermutlich als Handlaminat entstehen wird, muss ich über „vacuum bagging“ und „resin infusion“ noch nicht nachdenken.
Tag der Fehlschläge
22.11.2018 Der Plan war eigentlich, die beiden Röhren, die Rippen und die Montageplatte in der PU-Form mit Carbon zu füllen und die restliche Form mit einer Schicht EL2 „Epoxy Laminating Resin“ einzustreichen.
Die Rippen sollten mit einem Kohlefaserschnitzel-Harzgemisch gefüllt werden, in die Röhren wollte ich einen aufgerollten Streifen Carbon Gewebe stecken und diesen mit Harz tränken. In den Spalt, der negativ die Montageplatte abbildet, wollte ich schwere zusammengefaltete Carbon Gewebezuschnitte stecken und diese dann auseinander klappen. Der Montagebereich sollte zunächst besonders dick ausfallen und zum Bauteil hin langsam dünner werden.
Vorbereitend habe ich drei Streifen Carbongewebe mit 450 g/m² zu jeweils 95 mm Breite in 3 verschiedene Längen zu 180, 170 und 160mm geschnitten.
Außerdem habe ich versucht je einen Streifen von 1 cm Breite und 10 cm Länge zu schneiden. Aber, ein Streifen von 1 cm Breite lässt sich nicht aufrollen, weil er in seine Einzelfasern zerfällt.
Ich habe daraufhin den Plan mit den Rollen aufgegeben und wollte auch die Röhren mit angedicktem Harz (Kohlefaserschnitzel) füllen.
Also habe ich zwei Becher mit EL2 „Epoxy Laminating Resin“ vorbereitet.
Einen Becher mit 50 g Harz, dem ich ½ Teelöffel Kohlefaserschnitzel 3 mm zugesetzt habe um damit die Rippen und die Röhren zu füllen.
Und einen Becher mit 100g Harz, um damit die Form auszustreichen.
Beide habe ich mit AT30 Slow gehärtet. Die Raumtemperatur betrug knapp 21 °C. Die Topfzeit lag somit bei ca. 100 Minuten. Zeit genug also…
Ein halber Teelöffel Kohlefaserschnitzel macht aus 50 g Harz + 15 g Härter, also 75 g Ansatz, einen dicken Brei. Den habe ich mit einem schmalen Rührstab in die entsprechenden Stellen der PU-Form gefüllt. Mit einem Kunststoffspachtel habe ich dann die Zuschnitte in den Spalt gedrückt, die herausstehenden Seiten dann umgeklappt und mit Harz getränkt. Bis zu diesem Punkt war ich eigentlich mit dem Ergebnis recht zufrieden.
Dann wollte ich den Rest der Form mit einer Schicht EL2 einstreichen. Diese Schicht sollte einige Stunden härten, damit das Carbon Gewebe nicht direkt auf der Form liegt. Später dann, hätte ich im Vacuum-Bagging-Verfahren die Gewebelagen gegen die Form gezogen.
Die Form war mehrfach mit Meguiar’s #8 gewachst und mit Easy-Lease Trennmittel behandelt.
Hier begann das Problem:
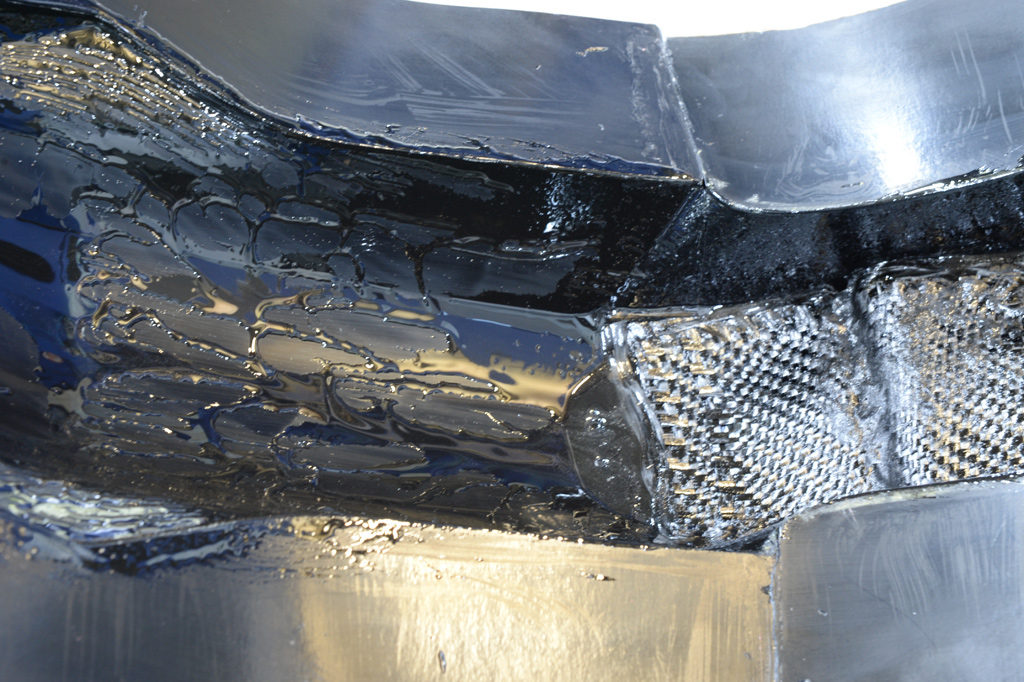
Das Harz bildete in der Form keine gleichmäßige Schicht, sondern perlte ab.
Ab jetzt wurde es stressig.
Ich wollte das so nicht aushärten lassen und habe daraufhin den Plan mit dem Vacuum-Bagging aufgegeben und versucht die Carbon Gewebe, beginnend mit dem 200 g-Gewebe als Sichtlage nass einzulaminieren. Das ist mir aber immer wieder nach innen gekippt und wollte sich auch nicht in den Knick am Rand des Bauteils legen lassen. Das war aber vorher schon klar. Frustriert habe ich dann alles weggestellt. Das muss jetzt mindestens 24 h aushärten, bevor ich den Mist entformen kann.
24.11.2018 Das misslungene Bauteil ist entformt. Aber es hängt noch jede Menge Harz in der Form. Das muss ich jetzt mit Hilfe meiner Fingernägel und mit weichen Kunststoffspachteln vorsichtig wieder entfernen, ohne die Form zu beschädigen. Aber, das dauert. Erst will das Harz nicht rein in die Form und jetzt will es nicht mehr raus. Es will das volle Programm: schaben knibbeln, Nassschleifpapier, Politur – die Finger tun schon weh und ein Ende ist noch nicht in Sicht.
Aber es gibt auch einen Lichtblick: Die beiden Röhren, die schmalen Rippen und die Anschraublippe sehen schon halbwegs brauchbar aus für das erste Mal. Der Rest ist Murks…
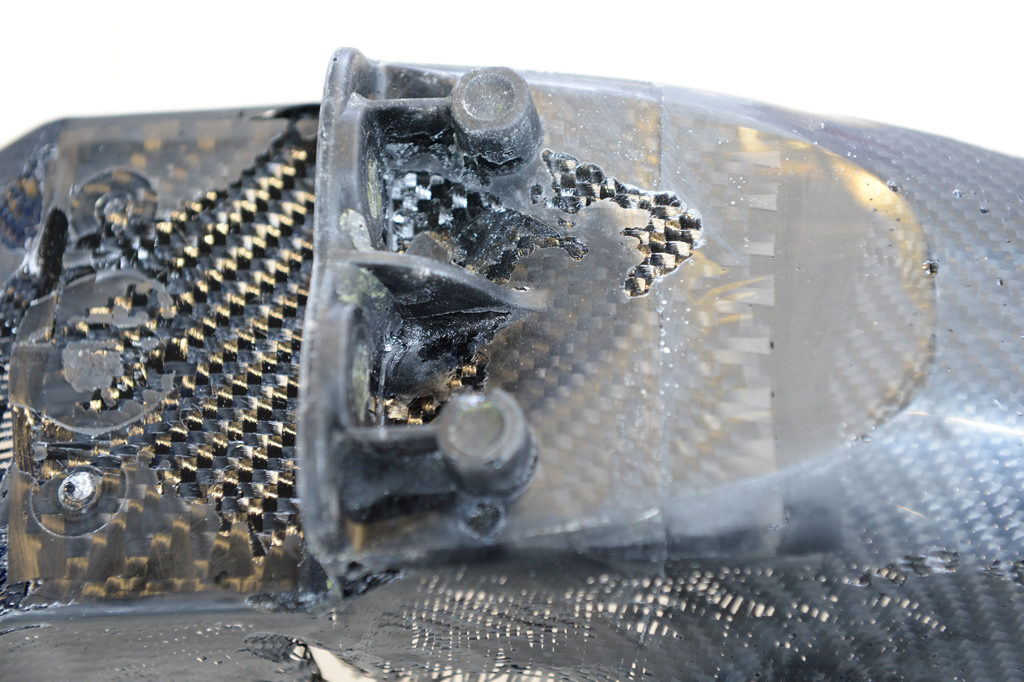
30.11.2018 Als würde es nicht schon reichen, die Fehlschläge ständig zu erleben, muss ich sie jetzt, wohl oder übel, auch noch bloggen. Aber, einmal angefangen, gehört das quasi dazu.
Im Betrieb war es heute relativ ruhig und die Form hatte ich während der letzten Tage ausreichend gereinigt, sodass ich einen neuen Versuch starten wollte.
Als Trennmittel hatte ich wieder EasyLease, also ein chemisches Trennmittel verwendet. Für das „Resin-Infusion-Verfahren“ sollte es das richtige Trennmittel sein.
Der Bereich mit den Verschraubungspunkten war bereits mit AFH-1 getrennt und ein Harz-Faserschnitzel Gemisch war eingefüllt und ausreichend gehärtet. Diesen Bereich habe ich zusätzlich mit einer Lage Gewebe verstärkt. Dieser Bereich ist später, am montierten Kotflügel, nicht sichtbar.
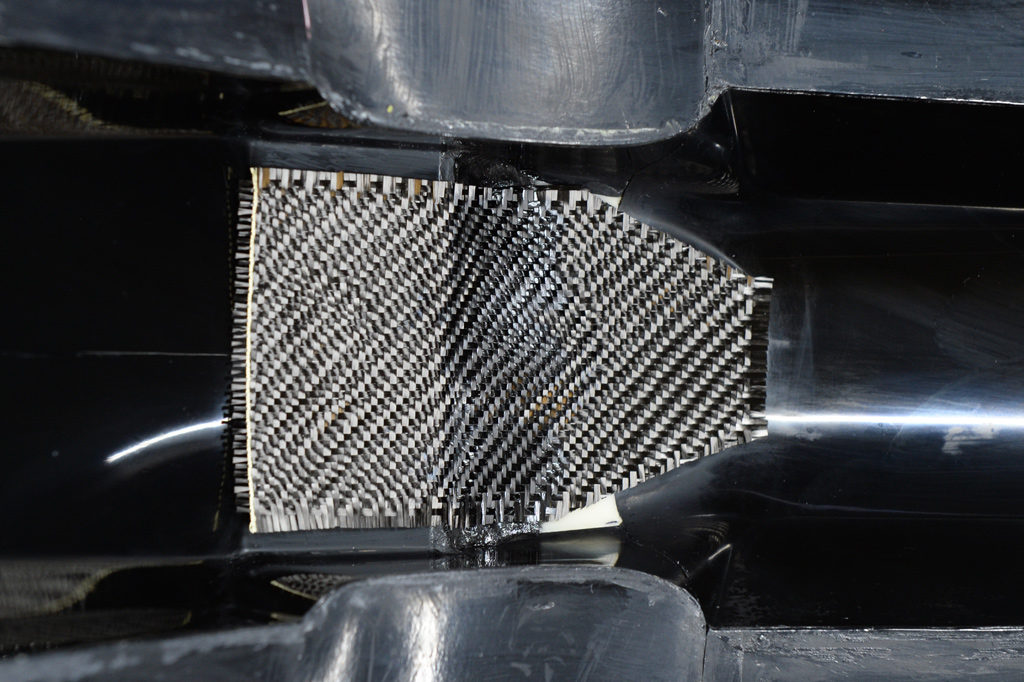
Ich hatte eine Schablone angefertigt, nach der ich Carbon-, Abreißgewebe und die Fließhilfe (Infusion-Mesh) zugeschnitten hatte. Alles lag bereits, mit Malertape fixiert, in der Form.
Aus Vakuumfolienschlauch (Vacuum Bagging Film) habe ich ein ausreichend langes Stück geschnitten und die ganze Form darin eingepackt. Die Schnittkanten habe ich beidseitig mit Vacuum Bagging Gum Sealant Tape verschlossen. Beide Anschlussstücke mit Schläuchen versehen, konnte ich gegen Mittag das erste Vakuum ziehen. Minus 28,5 inches HG war der höchste zu erzielende Wert. Das entspricht -960 mbar.
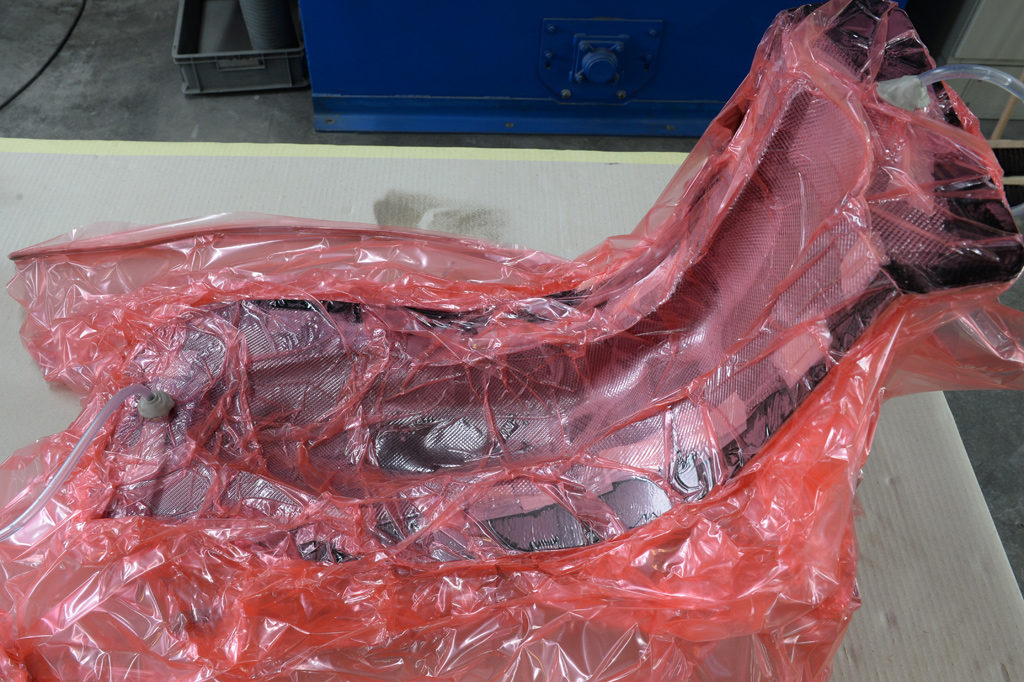
Aber: der Sack war nicht vollständig dicht und hielt dementsprechend das Vakuum nicht lange.
Ich habe dann ca. zwei Stunden lang nach undichten Stellen gesucht. Hörbar war nichts. Ich habe alle Klebestellen mit dem Daumen immer wieder nachbearbeitet und über alle Schrauben beidseitig zusätzlich Dichtband geklebt, aber die Undichtigkeit blieb.
Nach drei Stunden vergeblicher Bemühungen des Abdichtens, habe ich in halber Verzweiflung den kompletten Sack von außen mit Sprühkleber eingesprüht. Der Erfolg blieb jedoch aus.
Nach ca. vier Stunden habe ich einen zweiten Sack über den ersten gestülpt und auch diesen abgedichtet. Der Sack blieb jedoch undicht und ich war jetzt völlig down.
Gegen Abend habe ich dann einfach frustriert und todesmutig die Infusion gestartet und dabei „Banzai“ geschrien.
Davon kann ich aber, wie ich jetzt weiß, jedem nur abraten.
Ersten schreit man heute nicht mehr „Banzai“ sondern „Allahu Akbar“ und zweitens startet man keine Infusion in eine undichte Form.
Das Ergebnis ist wie erwartet fehlerhaft. Die Fasern lösen sich an den schwierigen Stellen mit den scharfen Knicken von der Form und es bilden sich Lufteinschlüsse (sog. bridging) weil der Druck fehlt.
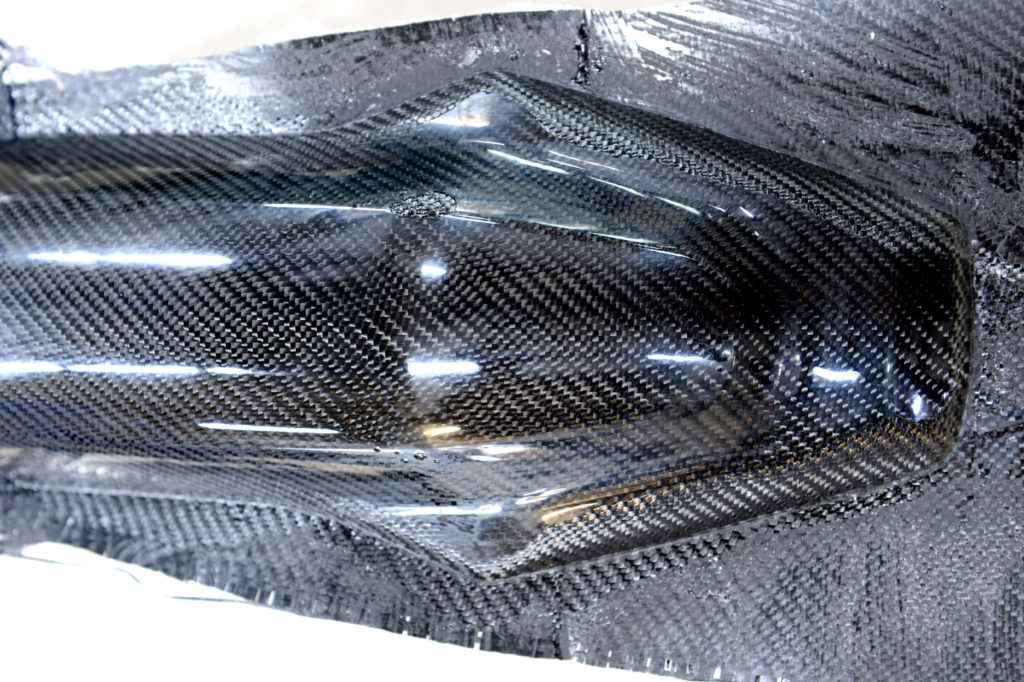
Ich habe mich ja zu Beginn des Projektes häufig negativ zum unangenehmen Geruch der Harze geäußert.
Es riechen allerdings nur die Komponenten aus dem „Uni-Mould Complete Mould Making Kit“ so stark.
Ist die Form erst mal gebaut, riecht es beim Herstellen der Teile kaum noch. Das Epoxy-Resin IN2 ist vom Geruch her kaum wahrnehmbar, der Härter AT30 riecht ein bisschen stechend nach Ammoniak, aber nicht aufdringlich. Man muss schon den Rüssel reinhalten in die Schüssel, damit es in der Nase sticht.
Formenbauer hat gepiercten Sack
07.12.2018 Ich habe inzwischen einen Verdacht was die Undichtigkeit meines „envelope vacuum bag“, also meines Vakuumsackes angeht. Ich habe mir nämlich an dieser Form häufiger in die Finger gestochen. Bei genauerer Untersuchung zeigen sich kleine, harzgetränkte Glasfaserstacheln, die aus dem ansonsten schön angelegten Laminat wehrhaft hervorschauen.
Stachelig war gestern
Obwohl ich sonst nicht so sehr auf „glatt rasiert“ stehe, bin ich allen Stacheln mit Schleifpapier auf den Leib gerückt. Anschließend habe ich die Außenseite der Formteile nochmal mit Epoxidharz angepinselt. Zusätzlich werde ich noch alle scharfen Kanten mit Tape abdecken.
Weil die letzte, misslungene, Infusion nur knapp 5 Minuten gedauert hat, habe ich heute gleich einen schnellen Ansatz angerührt und AT30 Fast als Härter gewählt. Das verkürzt die Zeit bis zum Entformen auf 4 bis 6 Stunden. Die Topfzeit ist für diesen Härter bei 25 °C mit 9 bis 14 Minuten angegeben.
Nach dem Schleifen und Entgraten der Form-Außenseite war nun nicht mehr damit zu rechnen, dass der Vakuumsack an irgendeiner Stelle durchstochen wird und das Vakuum war auch schnell auf 100 %.
Es gab zwei undichte Stellen, eine Falte zwischen Foliensack und Gum-Tape und eine Zweite am Schlauchanschluss der Infusionsseite. Beide waren schnell gefunden. Das Vakuum stand seit 30 Minuten sehr stabil.
Ich hatte den Infusionsschlauch mit Heißkleber in den Becher und den Becher auf dem Tisch festgeklebt. So konnte von der Infusionsseite her nicht mehr viel Unerwartetes geschehen. Da die Gesamt-Harzmenge bei der letzten Infusion sehr knapp bemessen war, habe ich diesmal ein bisschen mehr Harz angesetzt. 350 Gramm Harz plus 105 Gramm Härter AT30 Fast ergaben zusammen 455 Gramm.
Sehr zuversichtlich habe ich dann die Infusion gestartet. Leider wollte das Harz diesmal aber nicht so schnell in die Form wie beim letzten Mal. Die Form war nach ca. 30 Minuten zu etwa 75% getränkt, als das Harz im Becher mit seiner exothermen Reaktion begann. Und da noch locker 200 bis 250 g Harz im Becher waren, hat es auch gleich ordentlich geraucht, aus dem Becher. Anfassen konnte man den nicht mehr, so heiß war der.
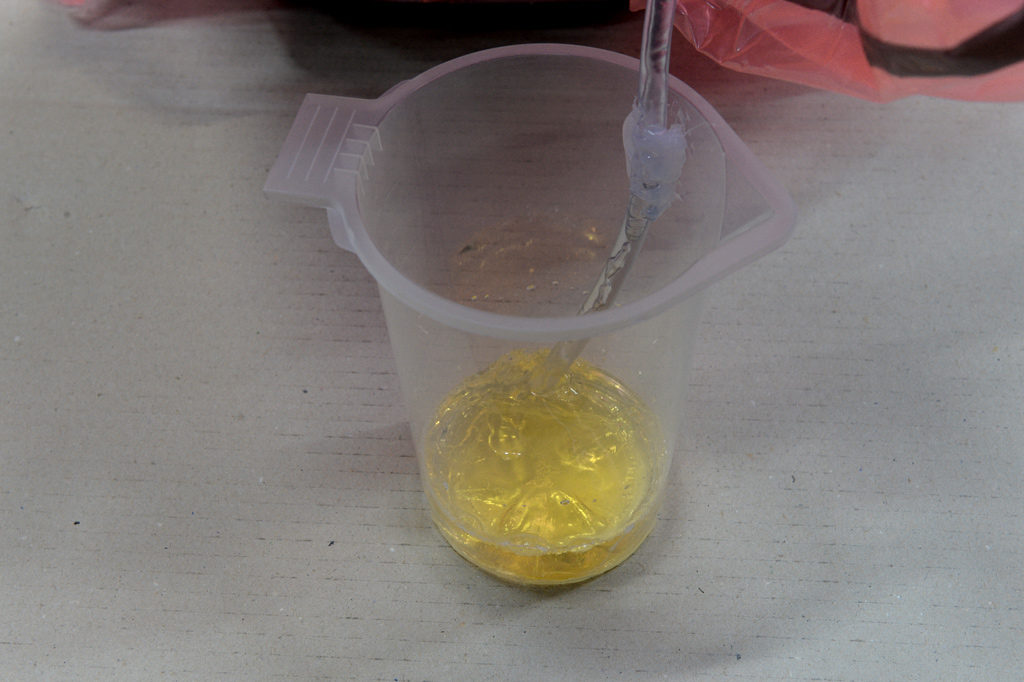
Eine spätere Messung zeigte immerhin noch eine Temperatur von 132 °C. Bei dieser Temperatur wird der Heißkleber schon wieder recht flüssig.
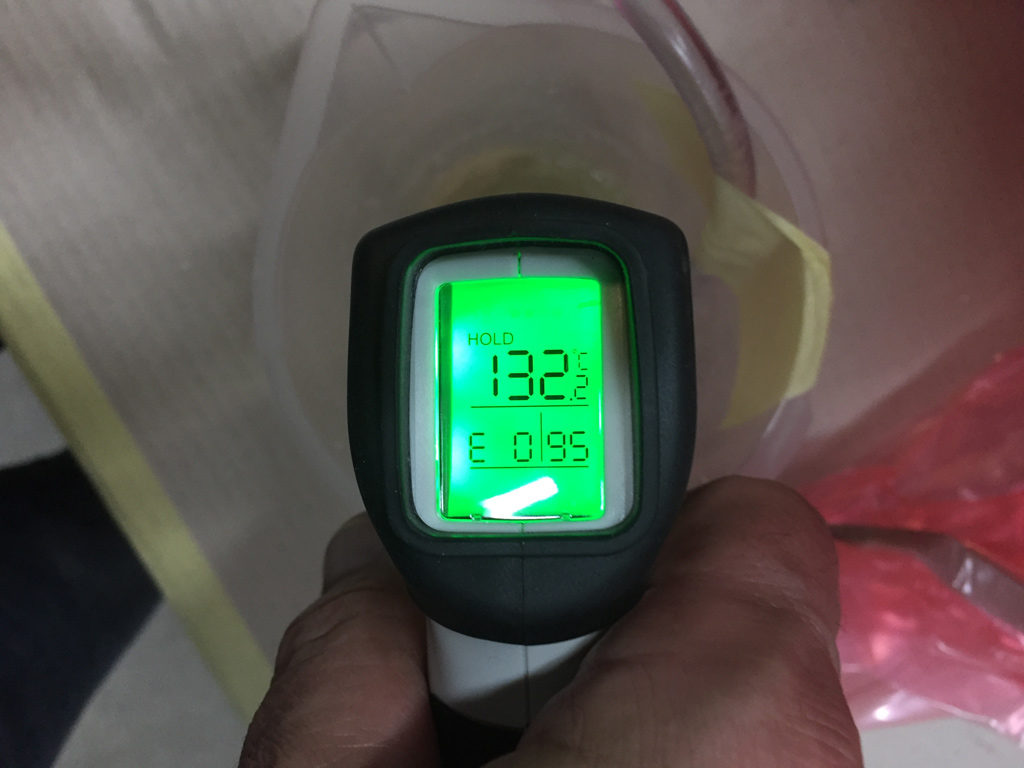
Das Harz im Schlauch hat aber noch zum vollständigen Tränken der Fasern gereicht, während es aus dem Becher die ganze Zeit lustig rauchte. Davon gibt es leider stressbedingt kein Foto. Die Infusion hat diesmal fast 40 Minuten gedauert. Um die letzten trockenen Stellen in der Form habe ich jede Minute gezittert.
Am nächsten Morgen konnte ich dann auch schon Entformen.
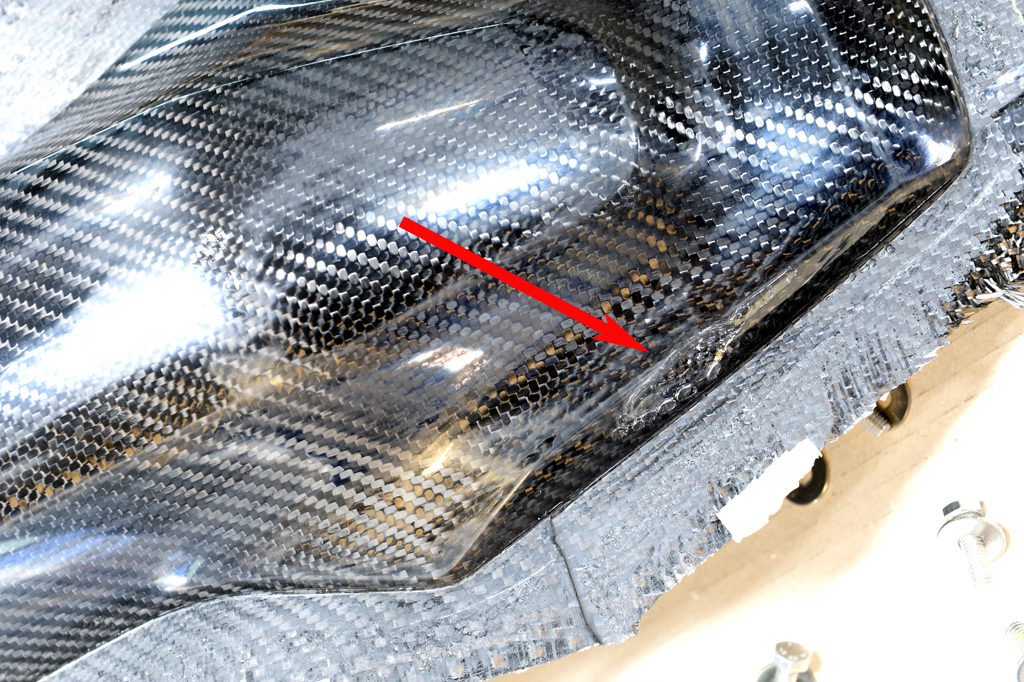
Schon wieder Müll produziert. So langsam reicht es mir.
Pilotserie
09.12.2018 Ein neuer Versuch. Vielleicht sollte ich auch mal anfangen zu „machen“ statt immer nur zu „versuchen“.
Also alles von Vorn. Geschliffene Form ohne Stacheln, Easy-Lease auf allen Flächen, alle Gewebe mit einem leichten Überschuss eingelegt, Infusions- und Vakuumseitig eine doppelte Lage Infusionsgewebe eingelegt, Härter-Mischung 2/3 Fast, 1/3 Slow angesetzt. Also 350 Gramm Infusionsharz IN2, 70 Gramm Härter AT30 Fast und 35 Gramm Härter AT30 Slow zu einer Gesamtmenge von 455 Gramm angerührt. Die Topfzeit sollte bei 25°C jetzt 43 Minuten betragen. Der Vakuumsack war auch gleich beim Ersten Drop-Test dicht. Das klappt mit ein bisschen Übung recht zuverlässig. Die Infusion hat knapp 25 Minuten gedauert.
10.12.2018 Das erste anständige Teil ist entformt. Kein „bridging“, keine Luftblasen. Die Oberfläche ist fast spiegelglatt. Leichte matte Stellen stammen vom Trennmittel und dürften sich relativ leicht wegpolieren lassen. Das Besäumen geht mit einer extra dafür angeschafften Wolframcarbid-Trennscheibe recht gut. Allerdings muss das Harz dazu sehr gut ausgehärtet sein, sonst schmiert es die Trennscheibe zu.
Am besten wartet man nach dem Entformen noch ein paar Tage. Man erkennt die vollständige Aushärtung daran, dass sich die harzgefüllten Infusionsschläuche wie Glas brechen lassen.
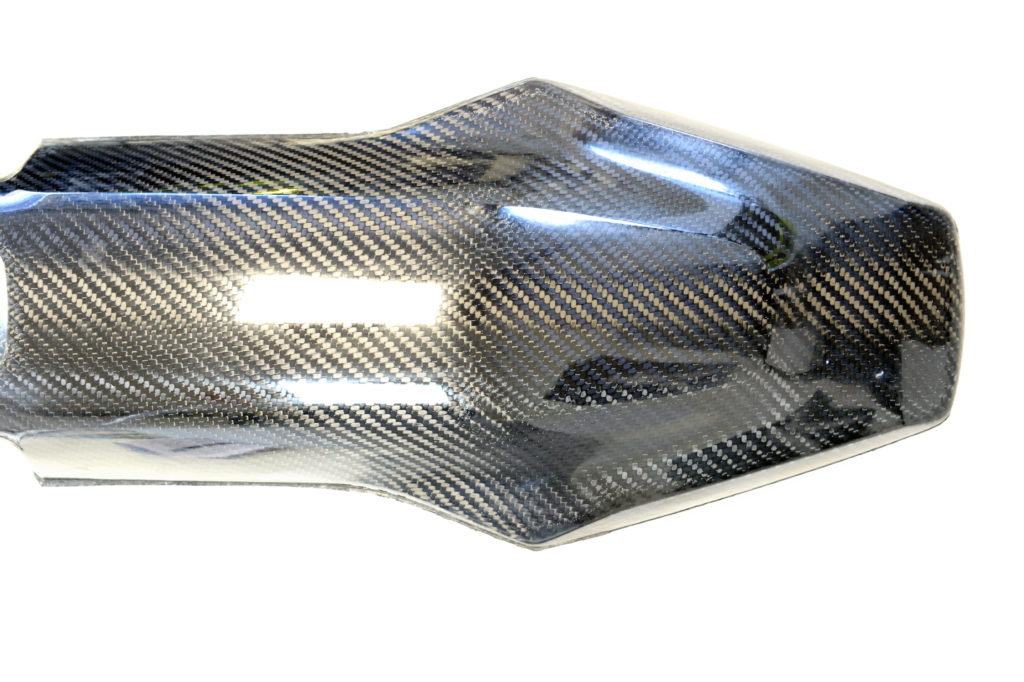
Leichte „Pinholes“ sind unmittelbar nach dem Entformen mit dem bloßen Auge kaum zu sehen. Sie sehen unter dem Mikroskop aus wie kugelige, angeschnittene Hohlräume, deren Öffnung zum Betrachter zeigt. Man sieht in diese Hohlräume hinein. Sie haben die Form von Wassertropfen auf poliertem Lack.
Erst bei der Politur oder beim Schleifen füllen sich diese mit dem weißen Schleifstaub oder dem flüssigem Träger aus der Polierpaste. Durch den Kontrast zum dunklen Hintergrund treten die Pinholes deutlicher hervor. Verwendet man eine spezielle schwarze Polierpaste wie z.B. „NW1 Super Cutting Compound Black“, verschwindet der Kontrast und die Pinholes werden fast unsichtbar.
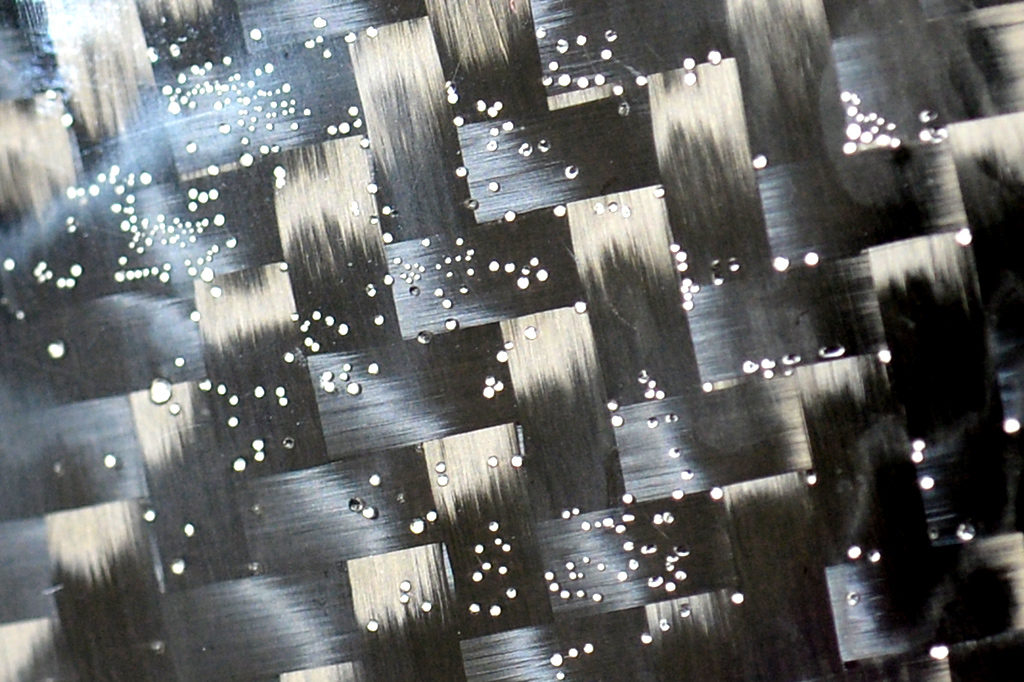
Fertig geschliffen und poliert wiegt der Front-Fender jetzt 278 Gramm und ist, von der Verstärkung im Bereich der Befestigung abgesehen, dabei 0,95 mm dick.
18.12.2018 Front-Fender No. 5: 50 Gramm IN2 + 15 Gramm AT30 Fast + ¾ Teelöffel “Chopped Carbon Fibre Strands”, Verstärkung Connector-Plate 650 g/m², 1 Layer 210 g/m², 1 Layer 650 g/m², Verstärkung Connector Plate 650 g/m², 1 Layer 210 g/m², Gesamtmenge Harz: 455 Gramm.
350 Gramm IN2 + 105 Gramm AT30 (80F+25S).
Mit Heißkleber den Infusionsschlauch in den Becher und den Becher auf eine Metallplatte geklebt. Unter die Metallplatte einseitig eine Leiste zum Schiefstand des Bechers angebracht. Nach der Infusion bleibt ein Rest von 100 Gramm im Becher. Die Wandstärke sollte jetzt 1,2 mm betragen und so ist es auch. Der erste fehlerfreie Carbon-Front-Fender ist produziert.
20.12.2018 Mit einer Borcarbid-Trennscheibe habe ich das Bauteil grob besäumt. Das Epoxidharz ist aber noch nicht voll durchgehärtet und schmiert mir die Trennscheibe wieder zu. Die Herstellerangabe ist ja auch 7 Tage für „fully cured“.
Mit einem 5 mm breiten Saum wiegt das Bauteil jetzt noch 339 Gramm. Ich kämpfe gegen meine Ungeduld und werde am Wochenende noch mal schleifen.
21.12.2018 Den Kampf gegen meine Ungeduld habe ich mal wieder verloren. Fertig geschliffen, gebohrt und poliert wiegt die verstärkte Variante No.5 jetzt 310 Gramm. Und so sieht No.5 am Motorrad aus nachdem das Dekor aufgeklebt ist:
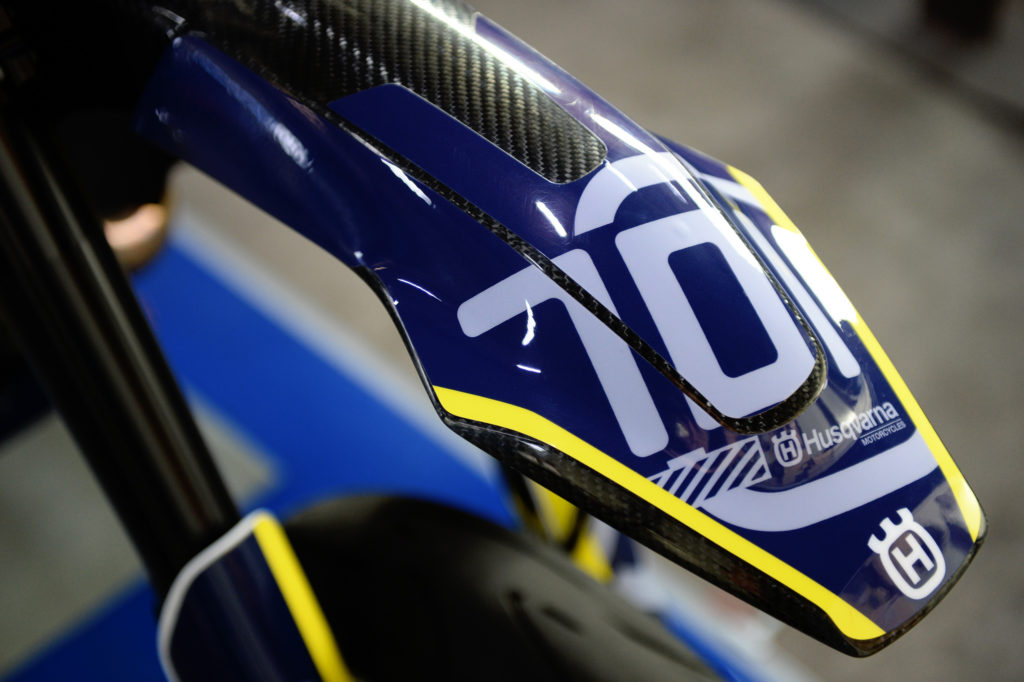
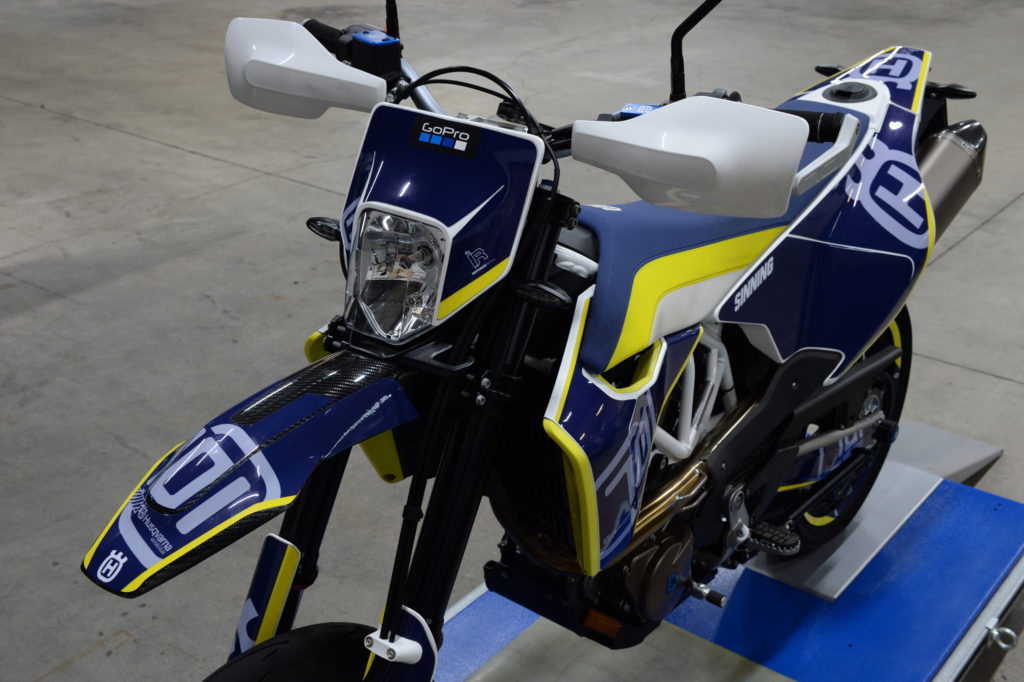
Montage Front-Fender Mark I
Die Form wurde vom originalen Front-Fender genommen, welcher als Spritzgussteil konstruiert wurde. Theoretisch hätte man ein neues Urmodell herstellen müssen, welches für die Abformung als Faserverbundwerkstoff-Bauteil optimiert ist. Ich habe diesen Schritt umgangen und dafür den Montagebereich verstärkt ausgeführt.
Zur Montage:
Der originale Kotflügel ist im Bereich der unteren beiden Schrauben 6,5 mm dick (8 – 1,5 = 6,5), der Carbon Front-Fender dagegen nur 2,5 bis 3 mm. Deshalb kürze ich die beiden originalen Schrauben für die Unterseite um 4 mm.
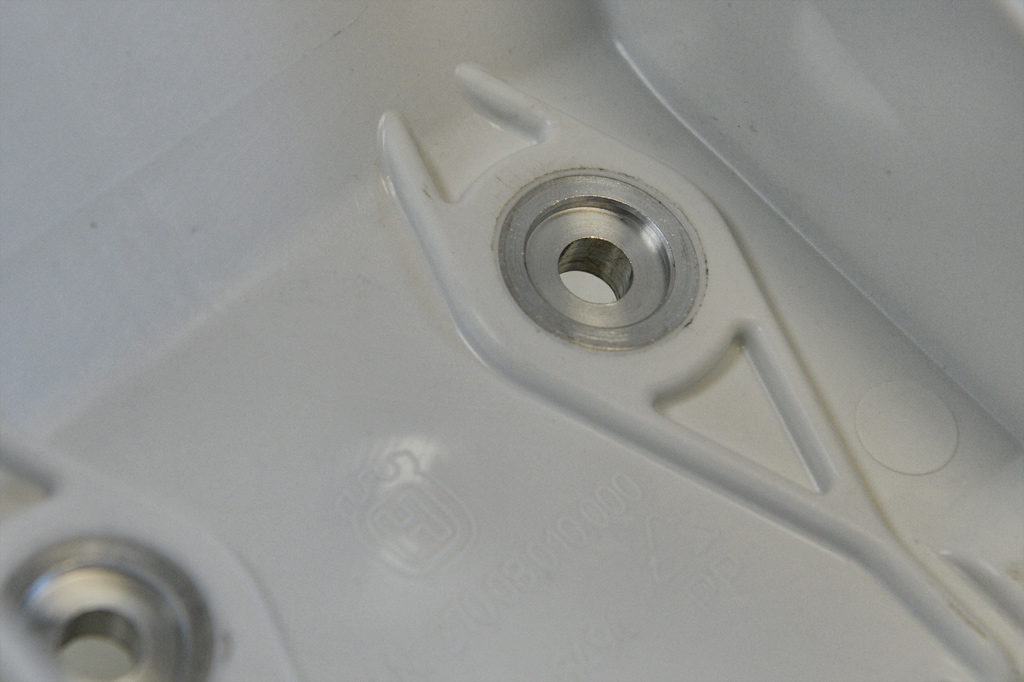
Es kann nicht schaden, die beiden Schrauben vor der Montage einmal ohne den Front-Fender von Hand bis zum Anschlag in die untere Gabelbrücke einzudrehen. Auf diese Weise merkt man erstens, ob man die Schrauben sauber gekürzt hat ohne die Gewinde zu beschädigen und zweitens, ob die Schrauben jetzt kurz genug sind und nicht an den Boden des Sackloches stoßen ohne den Carbon Front-Fender zu klemmen.
Für die Mark I Front-Fender nutze ich nur die beiden Montagepunkte, bei denen die Schrauben von unten durch den Kotflügel in die untere Gabelbrücke geschraubt werden. Zusätzlich verwende ich je eine größere Karosseriescheibe. Wie immer setze ich die Schrauben mit mittelfester Schraubensicherung ein. Die beiden vorderen Schrauben auf der Oberseite des Kotflügels werden bei den Mark I Front-Fendern nicht benutzt.
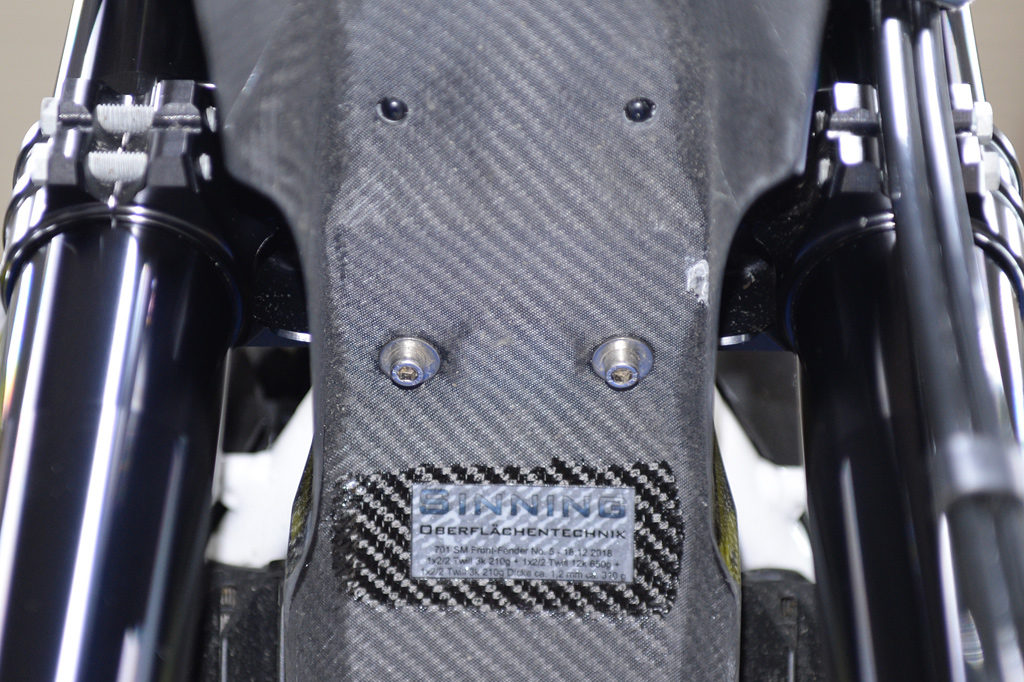
Die Front-Fender sind im Montagebereich ausreichend verstärkt um alle während der Fahrt am Bauteil auftretenden Kräfte über die unteren beiden Schrauben aufzunehmen.
Für die Montage des originalen Front-Fenders ist im Handbuch ein Drehmoment von 10 Nm angegeben. In Verbindung mit einer flüssigen mittelfesten Schraubensicherung sollte ein Drehmoment von 6 bis 8 Nm ausreichend sein.
Montage Front-Fender Mark II
Für die Montage der Mark II Front-Fender gilt das gleiche wie für die Mark I, mit der Ausnahme, dass alle vier Montagepunkte benutzt werden können. Die originalen oberen Schrauben passen hier ungekürzt.
28.12.2018 Das Projekt war eigentlich abgeschlossen. Ich hatte aber noch Harz und Carbonfasergewebe für ein paar Front-Fender mehr übrig. Also ans Werk! Ich experimentiere mit verschiedenen Härtermischungen aus AT30-slow und AT30-fast. Außerdem kombiniere ich verschiedene Carbonfasergewebe miteinander und versuche mit längeren Spiralschläuchen die Infusionszeit zu verkürzen. Im Idealfall kommt dabei jedes Mal ein brauchbarer Front-Fender raus.
01.01.2019 Die Ergebnisse der Feiertage zum Jahreswechsel:
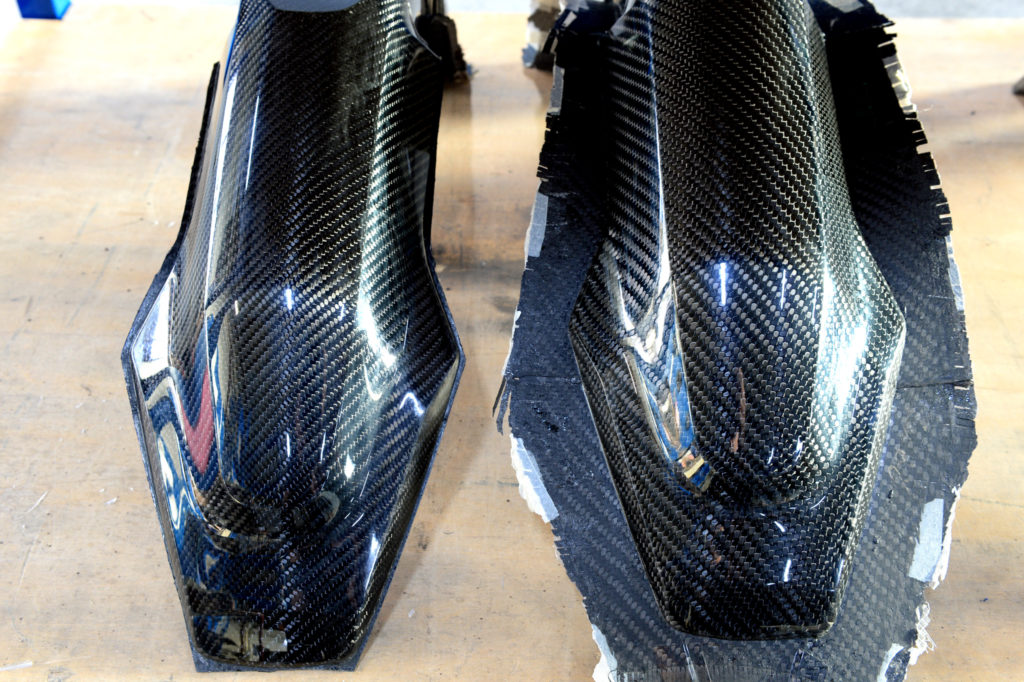
Front-Fender No. 6 im Bild links, bereits grob besäumt, bestehend aus: Sichtlage 1 x Carbon Fibre 2/2 Twill 3k 210g, Verstärkung 2 x Carbon Fibre 2/2 Twill 12k 450g. Gesamtstärke ca. 1,2mm.
Front-Fender No. 7 im Bild rechts, noch unbesäumt, bestehend aus: Sichtlage 1 x Carbon Fibre 2/2 Twill 12k 650g, Verstärkung 1 x Carbon Fibre 2/2 Twill 12k 450g. Gesamtstärke ca. 1,2mm.
03.01.2019 Auch das etwas gröbere 650er am Front-Fender No. 7 sieht, als Sichtgewebe verarbeitet, recht ansprechend aus. Beide Front-Fender sind inzwischen gebohrt und beschliffen, ordentlich stabil und bringen ein Gewicht von jeweils ca. 330 Gramm auf die Waage.
Übrigens habe ich während einer der letzten Infusionen die ersten paar Minuten mit der Kamera aufgezeichnet.
Bei der bisherigen Methode ist das Harz in den ersten paar Minuten noch relativ flott unterwegs. Dann wird es immer langsamer, je mehr bereits getränktes Gewebe zu durchdringen ist. Die gesamte Dauer der Infusion betrug im Fall des Bauteils aus dem oberen Video knapp 30 Minuten.
Ziemlich langweilig! Vielleicht mache ich bei einer der nächsten Infusionen mal ein neues Video.
Nullserie
Bei der Pilotserie habe ich vor der Infusion den Montagebereich noch mit angedicktem Harz gefüllt. Die auf diese Weise entstandenen Befestigungselemente waren jedoch relativ bruchanfällig. Deswegen wurden sie für die Montage auch nicht benutzt.
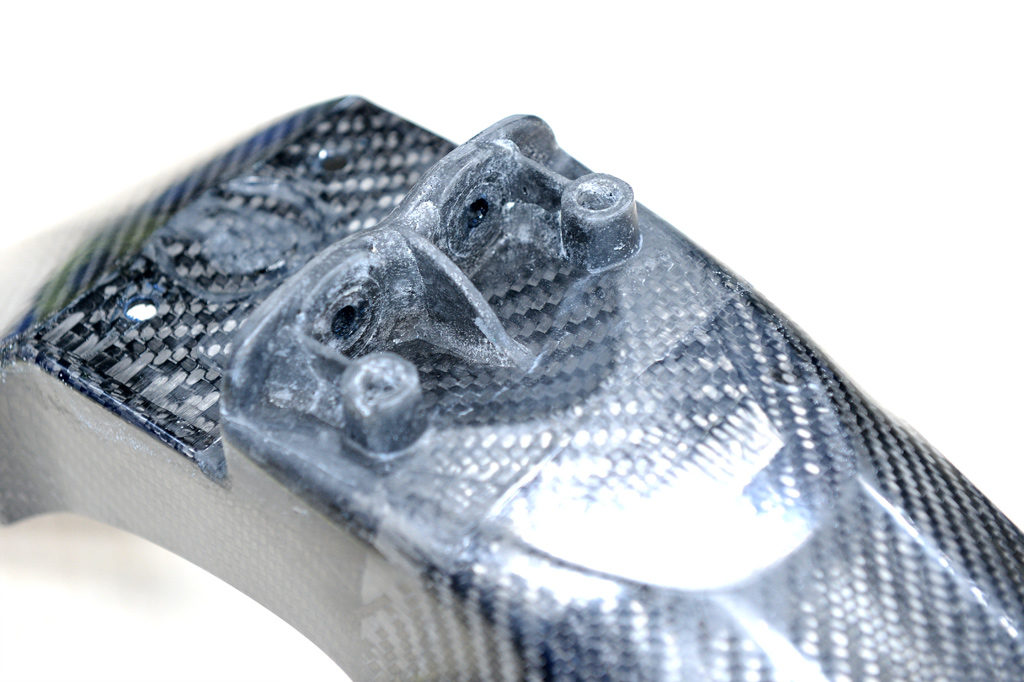
Jetzt lege ich den Montagebereich komplett mit Carbon-Gewebe aus. Genauso, wie man den Rest der Form beim Vakuuminjektionsverfahren auslegt.
Und das mit ordentlichem Ergebnis.
04.01.2019 Beim Front-Fender No. 8 habe ich gleich zwei Dinge verändert:
1. Der Montagebereich wurde nicht, wie sonst üblich, mit einem Gemisch aus Kohlefaserschnitzeln und Harz gefüllt, sondern ich habe den Spalt und die beiden Sacklöcher mit trockenem Gewebe ausgelegt und darauf gesetzt, dass die Fasern beim Infusionsprozess getränkt werden.
2. Ich verwende nun eine auf ca. 1,4 m verlängerte „Resin Infusion Spiral“ um kürzere Infusionszeiten zu erreichen.
Für die beiden zylindrischen Befestigungspunkte habe ich ein 650 er Gewebe einseitig leicht mit „Fusion Fix“ Sprühkleber eingesprüht und dann zwei ca. 15 mm breite Streifen davon geschnitten und diese aufgerollt. Sprüht man die Gewebe vor dem Schneiden nicht ein, so zerfallen sie in ihre Bestandteile.
Die so entstandenen Rollen habe ich in die Sacklöcher gesteckt. In den Spalt habe ich mit Hilfe eines Kunststoffspachtels zwei gefaltete Lagen 650er Gewebe gesteckt und dann zu beiden Seiten umgeklappt.
Danach habe ich weitere Gewebe in gewohnter Weise aufgelegt. Zusätzlich wurde, auch wie sonst üblich, der Montagebereich mit 3 Lagen 650er Gewebe verstärkt.
Durch die Verlängerung der „Resin Infusion Spiral“auf ca. 1,4 m konnte ich tatsächlich die Infusionszeit von bisher 30 Minuten auf knappe 7 Minuten verkürzen. Ich habe auch gleich ein neues Video gemacht.
Das kommt bald…
Und da ist es auch schon:
Mit diesem Ergebnis:
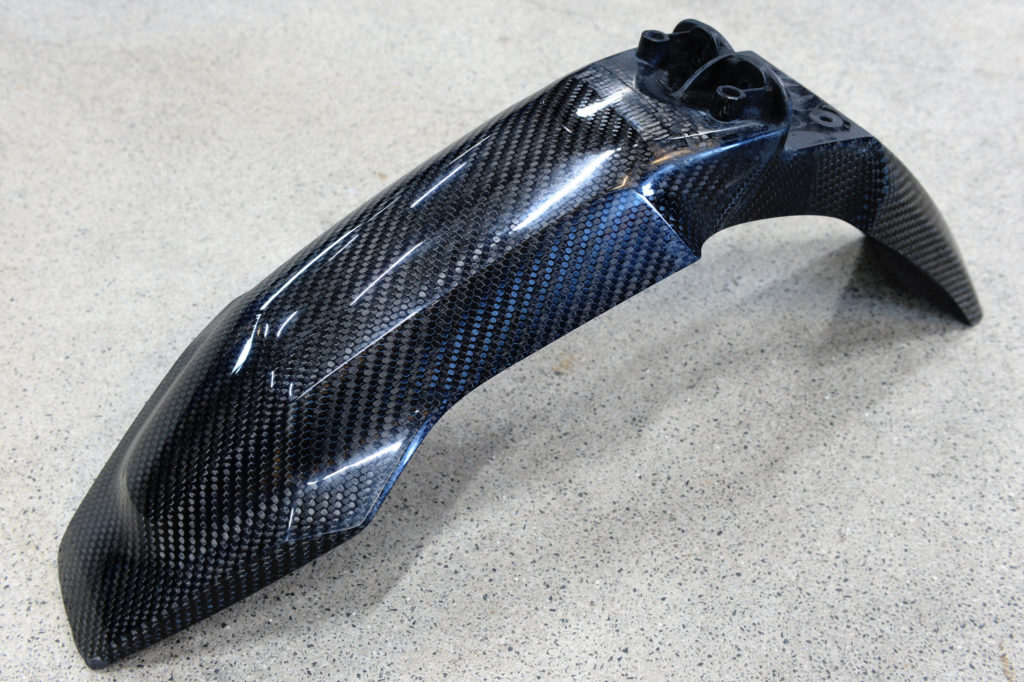
Generation Mark II
Stronger Parts by fully infused mountings
Der Montagebereich wird mit Carbon-Gewebe ausgelegt und bei der Infusion komplett mit Harz getränkt. Er ist jetzt genau so stabil, wie der Rest des Bauteils.
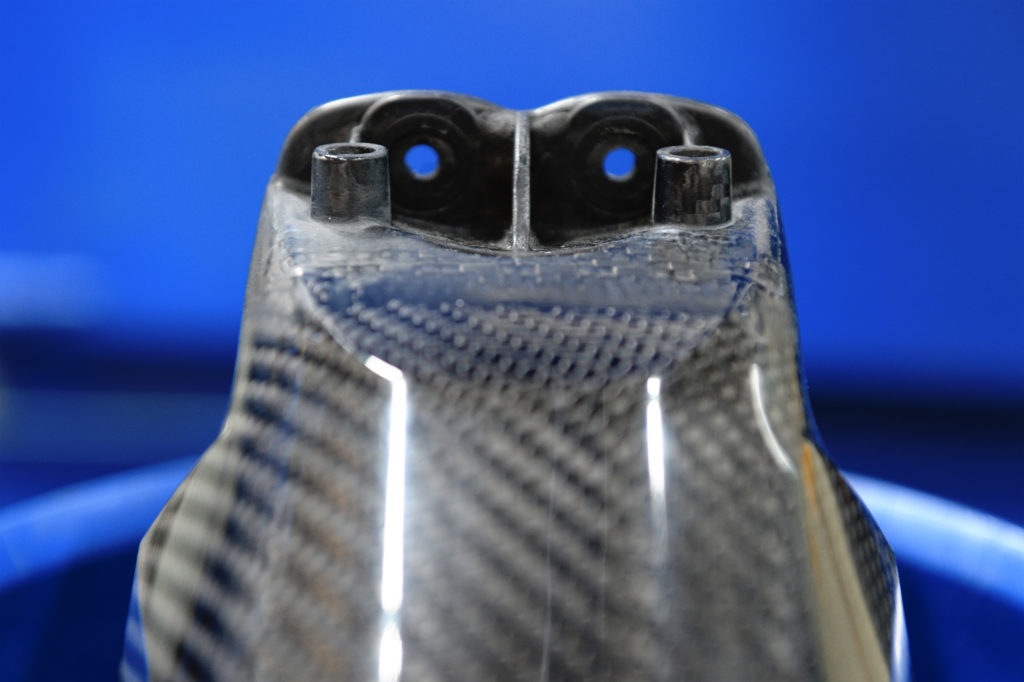
Jetzt wäre eine Montage über alle vier Verschraubungspunkte möglich und ich könnte die nächsten Kotflügel wieder dünner machen. Das ist aber nicht mein Ziel…
Schattenseiten
Damit nicht der Eindruck entsteht, hier würden nur raumfahrt-taugliche Carbonteile produziert: Es gibt auch ein paar nicht so schöne Stellen.
So hat die, dem Kühler zugewandte, Rückseite des Front-Fenders formbedingt eine Längsnaht. Die lässt sich allerdings, will man den Aufwand betreiben, auch wegpolieren.
Außerdem ist eine Überlappung der Gewebe im seitlichen Bereich (zwischen den Standrohren) sichtbar. Es tauchen auch immer wieder mal ein paar Pinholes auf oder eine kleine Luftblase auf der Rückseite.
Project Blue-Day Mark II
22.01.2019 No.10 Project Blue-Day Mark II
Eigentlich ist das Projekt schon lange abgeschlossen. Ich habe meine 701 mit einem schönen selbstgebauten Carbon Front-Fender ausgestattet und auch noch ein paar in Reserve produziert.
Aber dann bin ich bei EasyComposites auf ein blau durchwebtes Carbon gestoßen, mit dem ich noch eine „special Edition“ auflegen wollte.
Das blaue Gewebe ist aber sehr empfindlich. Die Fasern verschieben sich schon, wenn man es zu feste ansieht. Das ist dann für eine Form, die dem Gewebe alles abverlangt und es in alle Dimensionen verzerren will, eher nicht so gut geeignet.
Während man Unregelmäßigkeiten in schwarzen Carbonteilen fast suchen muss, fallen diese im blau durchwebten Carbon wegen des stärkeren Kontrastes sofort ins Auge.
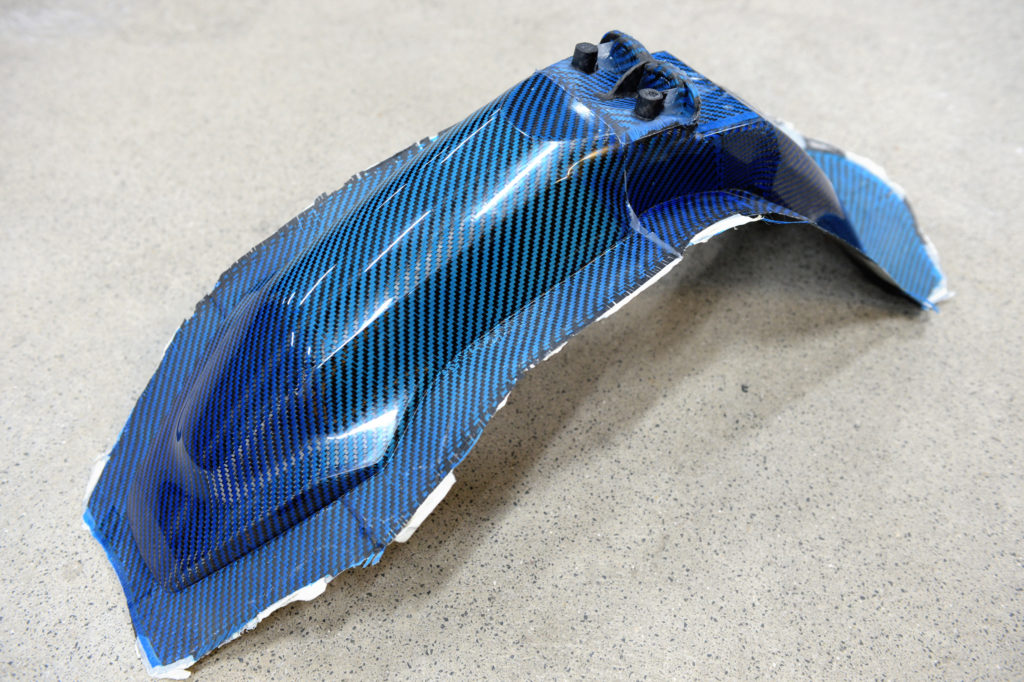
Und so sieht er aus, der Neue…
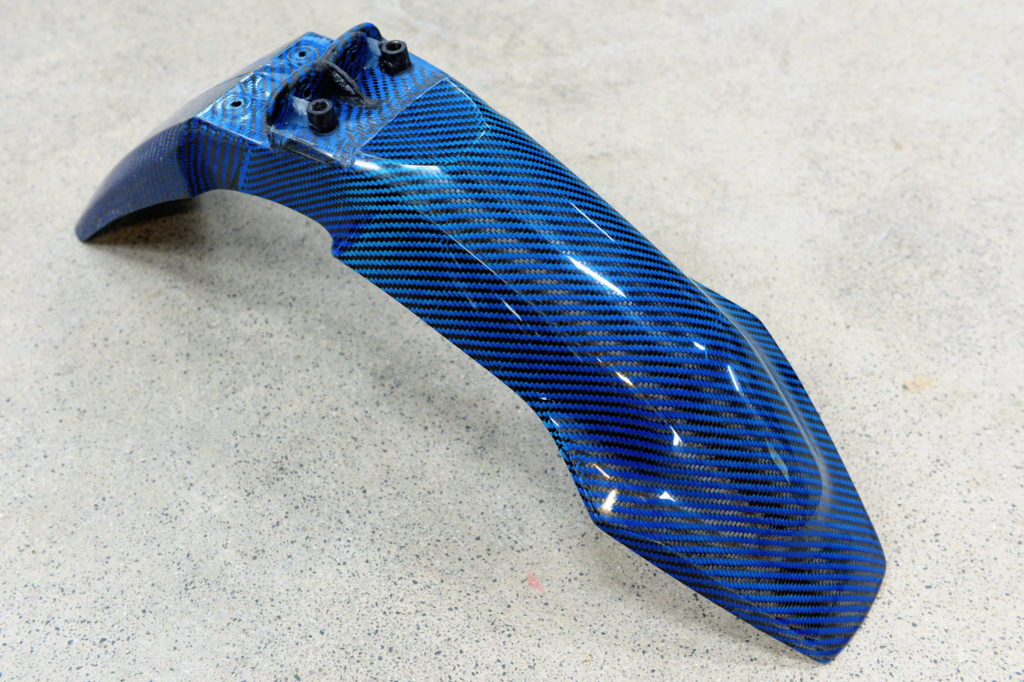
Hallo Frank,
ich muss am Ende dieser Woche wieder deine Durchhaltekraft loben. Oder sollte ich besser motivierend sagen „klappt ja eh nicht“.
Leider kann mein Kontakt dir nicht mit seinen 3D DruckScanSchneidetechniken aushelfen, da Carbon aufgrund seines Schmelz/Brennpunktes nicht behandelbar ist. Holz, Aluminium und oder Gips ließe sich in Form lasern. Aber auch hier müßte man einmal von oben schneiden, umdrehen und nochmal von oben lasern. Außerdem ist die Genauigkeit nicht so, dass man sich nachher darin spiegeln kann, was du ja wahrscheinlich machen willst.
Ich kann dir also nur anbieten, dich wieder mit zum Joggen zu nehmen, damit ich auch etwas von dem schönen Geruch mitbekomme.
Na dann bis zum nahen Termin
Gruß Jörg
Hello,
Hallo,
Wonderful job !
Is it possible to order 2 of them ?
Really impressive job !
It is for the swiss championship supermoto ! For 2 fs 450 !
Thanks in advance for your answer.
Peter
That is such an artisan work. I d like to buy this piece of art for my bike 🙂
Hallo
Eigentlich habe ich die Carbon Front-Fender nur für meinen eigenen Bedarf gemacht.
Es sind aber ein paar übrig. Mit dem Verkauf ist das so eine Sache.
Ich bin kein Händler und kann z.B. nicht für das Produkt haften, keine Garantie geben, die Teile nicht zurücknehmen usw.
Dafür sehen sie im Sichtbereich ordentlich aus und sind, im Gegensatz zu den meisten anderen die man irgendwo kaufen kann, im Montagebereich verstärkt.
Sie können einen Carbon Front-Fender auch bei einem Händler im Internet bestellen.
Dort kosten die 170,- € plus Versand und sehen hübsch aus.
Man hat sich dort leider nicht viele Gedanken über eine entsprechende Versteifung des Montagebereiches gemacht.
Dafür haben Sie dann aber alle Rechte wie Rückgabe usw.
Bei mir wäre eine Rückgabe ausgeschlossen.
Ich kann nicht das bieten, was Online-Händler Ihnen bieten können.
Meine Front-Fender sind auch optisch nicht immer zu 100 % perfekt.
Der Sichtbereich sieht jedoch meistens sehr gut aus.
Ich könnte Ihnen einen Front Fender schicken. Am besten kontaktieren Sie mich per Mail oder rufen mich dazu einmal an.
Aktuell könnte ich einen Mark-II mit 359 g und einen Mark-I mit 278 g abgeben. Siehe Bild
Mit freundlichen Grüßen aus Essen
Frank Sinning
Hi Frank,
sehe gerade Deine Fender. Geile Arbeit. Würde mir so ein Teil gerne an meine FS 450 schrauben. Das sollten die gleichen wie bei der 701 sein. Hätest Du da noch was? Würd mich freuen von Dir zu hören. Gruß Basti
hi Frank
Hast du noch was zum Verkauf fender mäßig für die 701 und noch mal verdammt krank was du da gezaubert hast
Mit freundlichen Grüßen domi
Hallo Domi,
lies bitte meinen Kommentar vom 04.10.2020.
Ja, ich habe noch einen Blauen und zwei Schwarze.
Bitte kontaktiere mich dazu per Mail.
L.G.
Frank
hallo frank,
hast du zufällig noch immer einen schwarzen korflügel zu verkaufen?
lg, andreas
Hallo Andreas,
ein paar habe ich hier noch.
Melde dich per Mail, oder ruf an.
L.G.
Frank